فرآیند جوشکاری لوله های بدون درز یا مانیسمان تولید نمی کند. فرآیند ساخت لوله های بدون درز در اواخر قرن نوزدهم توسعه یافت. علیرغم بسیاری از آزمایشها، آزمایشها و تکنیکهای قبلی، اختراع فرآیند لوله بدون درز چرخش متقاطع توسط برادران منسمن در اواخر دهه 1880 به طور گسترده به عنوان آغاز تولید در مقیاس بالا لوله بدون درز شناخته شد.
در فرآیند سوراخ کردن شمش، محور نورد موازی با محور شمش بخشی از فرآیند تولید است. این رول با چرخش در همان جهت یک مسیر مارپیچ برای عبور بیلت از شکاف رول ایجاد کرده است. علاوه بر این، سرعت خروجی حدود 10 برابر سرعت چرخش چرخ کاهش یافته است.
با معرفی یک هسته سنبله مانند که بین رول ها قرار می گیرد، می توان مواد گرد جامد را سوراخ کرد تا با غلتاندن و غلتش همزمان در حین گرم شدن، یک پوسته توخالی تشکیل شود. اما هنوز نمی توان لوله هایی با ضخامت دیواره معمولی در طول مورد نیاز را تنها با سوراخ کاری و فرز تولید کرد.
تنها پس از توسعه و معرفی یک فرآیند شکل دهی ثانویه، “فرایند نورد” (دوباره توسط برادران مانیسمن)، امکان تولید لوله های فولادی بدون درز فراهم شد. فرآیند شکلدهی کششی نیز یک فناوری غیرمعمول و نوآورانه بود، که در آن لولههای توخالی با دیواره ضخیمتر باید توسط یک فرآیند نورد (یا با استفاده از قالبها) به لولههای نازک کشیده شوند که روی سنبه قرار میگیرند تا زمانی که فرآیند خاموش کردن کامل شود و بیلت تبدیل شود. یک لوله بدون درز
در حال حاضر لوله بدون درز (Mannisman) از صفحات گردی ساخته می شود که در مرکز سوراخ شده و پوسته توخالی ایجاد می شود و سپس به اندازه دلخواه نورد یا فشرده می شود. فرآیند تولید لوله بدون درز شامل مراحل اصلی زیر است.
تولید پوسته لوله توخالی در عملیات آسیاب یا اکستروژن
پانل لوله ای توخالی با کاهش قطر و ضخامت دیواره کشیده می شود
ساخت لوله نهایی در فرآیند نورد سرد یا گرم
از آنجایی که معلوم می شود این فرآیند تولید بدون جوشکاری است، لوله بدون درز (Mannismann) قوی تر و قابل اطمینان تر است. لوله های بدون درز نسبت به سایر لوله ها در برابر فشار پایدارتر و بهتر هستند.
زمانی که انحصار این فناوری به پایان رسید، تحولات مختلفی در فرآیند تولید رخ داد و مراحل شکلگیری آنها در فرآیندهای جدید ادغام شد. امروزه فرآیندهای تولید لوله بدون درز در سطوح مختلف تکامل یافته و این فرآیندها به فرآیندهای مدرن با کارایی بالا تبدیل شده اند.
بسته به اندازه لوله، ترکیب محصول و در دسترس بودن مواد اولیه، کارخانه های جدیدی برای تولید لوله های بدون درز ساخته شده است.
یک فرآیند نورد و سنگ زنی مداوم در محدوده اندازه گیری از حدود 21 میلی متر تا 178 میلی متر انجام می شود.
شمش توسط یک فرآیند سنبه چند لایه با سنبه های استوانه ای آویزان با قطر خارجی 140 میلی متر تا 406 میلی متر توخالی می شود.
فرآیندهای نورد و فرز چرخشی در اندازه های 250 تا 660 میلی متر وجود دارد. علاوه بر این، فرآیندهای جدیدی مانند آسیاب چرخشی که در قالب فرآیند Assel و Diescher یا فرآیند پرس لوله از پرس Everhart توسعه یافت، توسعه یافت. یک فرآیند معمولی تولید لوله بدون درز در شکل 1 نشان داده شده است.
فرآیند سنگ زنی و پانچ برای تشکیل لوله
فرآیند سنگ زنی و پانچ برای ایجاد شکل لوله
شکل 1 – فرآیند سنگ زنی و پانچ برای ساخت لوله
ساخت لوله بدون درز
در این فرآیند شمش ها در کوره دوار تا دمای 1250 تا 1300 درجه سانتیگراد گرم می شوند. قبل از کوره، شمش ها با فشار آب تمیز می شوند و به واحد حفاری سنبه منتقل می شوند و در آنجا یک شمش خشن با پوسته ضخیم تولید می کنند.
در این فرآیند اولین محصول خام 1.5 تا 2 برابر طول می کشد و سطح مقطع آن بین 33 تا 50 درصد کاهش می یابد. دکل حفاری متشکل از دو برش چرخشی است که مخصوص کشیدن لوله طراحی شده اند که در یک جهت چرخش هدایت می شوند.
محورها 3 تا 6 درجه از خط افقی چرخش هستند. فضای بین بلوک ها معمولاً توسط یک بلوک پشتیبانی غیرقابل کنترل در بالا و یک بلوک پشتیبانی در پایین بسته و بسته می شود. یک نقطه فرز، که به عنوان یک ابزار داخلی عمل می کند، در مرکز شکاف رول قرار دارد و توسط یک بلوک رانش خارجی از طریق یک هسته سنبه مانند در مرکز قرار می گیرد.
سپس پوسته توخالی و دیواره ضخیم برای تکمیل لوله سوراخ می شود و سپس سوراخ دوباره در محل سوراخ سوراخ می شود. نسبت ازدیاد طول در فرآیند تف جوشی بین 5 تا 10 است که با کاهش سطح مقطع 80 تا 90 درصد همراه است.
یک خط پانچ از دو پانچ (که گاهی اوقات به دلیل فشار دادن قالب نامیده می شود) با شکل مخروطی در اطراف پانچ تشکیل شده است. غلتک ها با حرکت عرضی مواد اولیه سازگار هستند. دمای کار در اطراف قالب ها بین 200 تا 220 درجه است و شامل یک ورودی مخروطی، یک استوانه و یک تخت است که برای آزاد کردن قطعه کار در یک محفظه بزرگتر قرار می گیرد. شکل دهی یک فرآیند خمشی آهسته است که با چرخش قطعه به جلو و عقب کار می کند.
پس از اتمام فرآیند مهر زنی یا شکل دهی، لوله تمام شده از سنبه خارج می شود. قسمتی از پوسته توخالی را برش می گویند. پس از گرم شدن در کوره، لوله به اندازه مناسب در خط نورد کاهش می یابد. دستگاه فرز قطر خارجی دقیقی ایجاد می کند و غلظت و چرخش لوله را افزایش می دهد.
معمولاً سه بخش و دو یا سه چراغ بزرگ دارد. غلتک ها دارای یک ضربدر بسته (در تنظیمات چند ایستگاهی) هستند که زاویه ای را نسبت به خط غلتک جلو تعیین می کند.
با انقباض یا کشش نورد، قطر خارجی لوله به طور قابل توجهی کاهش می یابد و ضخامت دیواره کمی افزایش یا کاهش می یابد. بسته به نوع محصول، کارخانه ها دارای 5 تا 28 مرحله نورد هستند.
پس از آخرین عملیات شکلدهی، لولههای تمام شده در بستر خنککننده تا دمای محیط خنک میشوند و پس از بازرسی دقیق به بخش تکمیل منتقل میشوند، جایی که فرآیندهایی مانند ماشینکاری انتهای لوله، صاف کردن و آزمایش هیدرولیک انجام میشود.
برای لوله های با قطر بزرگ که مواد ورودی معمولاً ریخته گری چند ضلعی است استفاده می شود. این قطعه پس از گرم شدن در کوره دوار ابتدا با سنبه عمودی در قالب دایره ای قرار می گیرد. قطعه کار سخت شده با یک پانچ استوانه ای به اندازه نصف قطر سوراخ فشرده می شود که پایه آن یک پوسته توخالی بسته را تشکیل می دهد.
عملیات بعدی شامل کاهش ضخامت دیواره با درجه کمی از گسترش طول لوله در چرخش است. در طی این فرآیند، انتهای لوله سوراخ می شود. پس از آن پوسته توخالی شکل لوله را روی خط ابزار شکل دهی می گیرد و سپس عملیات اندازه گیری و برش انجام می شود.
فرآیند نورد پلاگین یا فرآیند کشیدن
پلاگین فرآیند گمرکی یا فرآیند مالیاتی
فرآیند رول پلاگین یا فرآیند قرعه کشی
فرآیند نورد توپ برای رول صاف لولههایی با قطر 60 تا 406 میلیمتر با ضخامت دیوارههای بین 3 تا 40 میلیمتر و طول لولهها از 12 تا 16 متر استفاده میشود. در این خط، فرآیند حفاری یک مرحلهای یک پوسته توخالی جدار نازک با طول 3 تا 4.5 برابر طول اولیه و درجه تغییر از 65 تا 75 درصد ایجاد میکند.
خط فرز دارای دو چرخ جلو است که دارای گذرگاه دو طرفه است. محورهای کلتاک موازی با خط عمودی است و از 6 درجه تا 12 درجه از افقی متغیر است. شکاف بین رول های کار با استفاده از راهنماهای بالا و پایین تنظیم می شود.
این کفش های راهنما به فرآیند کشیدن کمک می کند و به عنوان نگهدارنده پین عمل می کند، بنابراین می تواند یک پوسته توخالی نازک ایجاد کند. محصولی که از قالب بیضوی عبور می کند از خط نورد پیروی می کند و به سنبه اجازه می دهد تا به طور موثر به عنوان یک ابزار داخلی برای تشکیل لوله عمل کند.
با توجه به زاویه شیب نسبتاً زیاد غلتک و سرعت بالای نورد، سرعت خروجی محصول بسیار سریع است. افزایش عمر سنبه بسیار مهم است. در مورد لوله های با قطر بزرگتر، قبل از اتصال به توپی، یک سنبه ثانویه (به نام آلوگاتور) وجود دارد.
سنبه های جدید فقط یک قسمت مخروطی شکل برای سوراخکاری با پین های کاری دو سطحی دارند، زیرا هر یک از آنها با محصول تولید شده زاویه حدود 30 درجه دارند. و به صورت مورب 10 تا 12 درجه از افق فاصله دارند. شکاف چرخش توسط دو دیسک جانبی که متحرک نیز هستند بسته می شود
فرآیند نورد مداوم
پس از برداشتن سنبه، لوله های چرخانده شده قبل از پردازش روی خط اندازه یا برش یا کشیده شدن دوباره گرم می شوند. آسیاب که از نظر ساخت شبیه به آسیاب پیوسته است از دوازده آسیاب تشکیل شده است.
کاهش فشار یک تکنیک منحصر به فرد است زیرا بدون استفاده از مهاربند و نگهدارنده سنبه، ضخامت دیواره کاهش می یابد و قطر لوله نیز کاهش می یابد. نیروی کششی اعمال شده به لوله نه تنها در کاهش ضخامت دیواره لوله موثر است، بلکه کاهش قطر ایجاد شده در هر مرحله را می توان سه برابر کرد.
در تصویر زیر 4 مرحله غلتاندن و کوبیدن برای ایجاد پوسته ساخته شده پس از آسیاب را مشاهده می کنید که پس از اتمام فرآیند سوراخ در این مرحله به تدریج شکل و فرم لوله را به خود می گیرد. تبدیل به یک دایره کامل می شود.
فرآیند رول پلاگین یا فرآیند کشیدن
کاهش و اندازه برای لوله های با قطر کمتر استفاده می شود. حفاری لوله های با قطر کوچک؛ زیرا نورد و برش به صرفه نیست. تولید لوله های نورد گرم با قطر 75 میلی متر نیاز به فرآیند کاهش و اندازه گیری ماشینی خاص دارد. این دستگاه شبیه یک خط نورد پیوسته است. این ترکیب از 8 تا 16 مرحله شامل 2 غلتک با نوارهای بلند به قطر 305 میلی متر تشکیل شده است.
برای قطرهای حدود 140 میلی متر یا بیشتر، اندازه گیری هایی برای اطمینان از اندازه و چگالی لوله در طول لوله انجام می شود. بنابراین، فرآیند اندازه گیری فقط شامل عبور لوله از دو یا سه پین غلتکی است که شیار کمی کوچکتر از شیار لوله غلتکی است. در برخی موارد، توانبخشی ضروری است.
در برخی موارد، نورد و چرخش با فرآیندهای معمولی، یعنی نورد پیوسته، به عنوان مثال با 9 تکیه گاه جداگانه از رول های شکاف بلند جایگزین می شوند. پس از نفوذ یک قطعه توسط خط فرز، سنبه روانکاری به طور قابل توجهی بزرگتر از پوشش سوراخ شده وارد می شود و هر دو از خط نورد عبور می کنند.
فرآیند نورد پیوسته شامل عبورهای متعدد شمش از یک سری رول های چرخان برای تشکیل خط نورد است. این نوع نورد، پوسته توخالی که روی خط فرز سوراخ شده است را می کشد و توسط سنبه ای که به عنوان ابزار داخلی عمل می کند، لوله به شکل نهایی خود در می آید.
فرآیندهای جدیدتر از چرخ سنگ زنی به جای سنبه های شناور آزاد به عنوان طرح کنترل استفاده می کنند. مزیت این نوع عملیات این است که برای تولید سنبه به درختان کمتر و کوتاه تری نیاز است. این نوع فرآیند تولید مداوم به عنوان تولید خط لوله (MPM) نیز شناخته می شود.
mpm
آب بندی لوله چند مرحله ای (MPM) بخشی از فرآیند چرخاندن گرمای لوله های بدون درز در یک ژاکت پوشش داده شده است. این سوله ها معمولاً از 8 پایه دو بلوک منحنی ساخته می شوند که با زاویه 90 درجه نسبت به یکدیگر قرار می گیرند. مصالح ساختمانی بر روی سنبه سرد و روغن کاری شده سوار شده و در اولین ورقی که نورد شروع می شود فشرده می شود. سنبه با سرعت ثابت در فرآیند MPM حرکت می کند. سپس یک لوله برش داده می شود، کالیبره می شود، آماده می شود و قبل از حمل و نقل بازرسی می شود.
با این فرآیند می توان به حداکثر طول رسید. طول لوله تولیدی تا 30 متر می باشد. تغییر شکل و عدم گرد بودن می تواند کمتر از 10٪ باشد.
اگر تا زمانی که سنبه کشیده شود از نورد پیوسته استفاده شود، دمای لوله تا حدود 500 درجه سانتیگراد کاهش می یابد. لوله از 950 تا 980 درجه سانتیگراد دوباره گرم می شود و سپس در یک رول کاهش می یابد.
نورد کاهشی و کششی ممکن است شامل هر تعداد رول یا بیشتر باشد، از 24 تا 28 ایستگاه، که همگی با هم فاصله دارند تا یک خط را تشکیل دهند. هر پایه موتور درایو یا سرعت متغیر خود را دارد و با سه براکت نصب با قطر کوچک کامل می شود. سه کلتکس با هم یک جاده مواج را تشکیل می دهند که از ایستگاهی به ایستگاه دیگر کوچکتر و کوچکتر می شود.
در این لمینیت از مواد داخلی استفاده نمی شود و سرعت غلتک ها از ورود تا خروج به طور مداوم افزایش می یابد.
چندین فرآیند دیگر در اجرای یک لوله بی پایان وجود دارد. این فرآیندها شامل فرآیند پرس، فرآیند پانچ و کشش، فرآیند اکستروژن لوله و فرآیند برش متقاطع است. فرآیندهای تراش متقاطع شامل فرآیند چرخش مارپیچی و فرآیند چرخش قالب می باشد. علاوه بر این، لوله های صلب نیز با فرآیند شکل دهی سرد، کشش سرد و فرآیند شکل دهی رول سرد تولید می شوند. در تصویر بالا نمای کلی و خلاصه آسیاب را به صورت چرخشی برای رسم پوسته خالی ساخته شده برای رسیدن به قطر مورد نظر مشاهده می کنید.
ساخت لوله بدون درز با شمع نورد یا فرآیند کشیدن
لوله های بدون درز یا دوتایی در فرآیند جوشکاری تولید نمی شوند. فرآیند تولید لوله های بدون درز در پایان قرن نوزدهم توسعه یافت. علیرغم بسیاری از آزمایشها، آزمایشها و فنآوریهای قبلی، اختراع فرآیند اتصال عرضی لولههای بدون درز توسط برادران منسمن در اواخر دهه 1880 به طور گسترده به عنوان آغازی برای تولید لولههای بدون درز برتر شناخته شد.
در فرآیند حفاری پایه، محور نورد موازی با محور پایه بخشی از فرآیند تولید است. این چرخ با چرخش در یک جهت یک مسیر دایره ای برای عبور بیلت از شکاف ایجاد می کند. علاوه بر این، سرعت خروجی به حدود 10 برابر سرعت چرخش چرخ کاهش می یابد.
با قرار دادن یک پایه سنبه مانند در شکاف بین رول ها، می توان مواد نورد جامد را در حین نورد گرم تزریق کرد تا با غلتیدن و چرخاندن با هم یک پوسته توخالی تشکیل شود. با این حال، هنوز نمی توان لوله هایی با طول دلخواه با ضخامت دیواره استاندارد را تنها با فرآیند حفاری و فرز ساخت.
تنها پس از توسعه و معرفی فرآیند شکلدهی ثانویه، «فرایند نورد» (دوباره توسط برادران مانیسمن)، میتوان لولههای فولادی تولید کرد. فرآیند نورد دیوار ضخیم شده (یا قالب) به لوله های نازکی کشیده می شود که تا زمانی که فرآیند برش کامل شود و بالش به یک لوله پایدار تبدیل شود، در یک سنبه قرار می گیرند.
در حال حاضر لوله بدون درز (Mannisman) از صفحات گرد ساخته می شود که از وسط سوراخ شده و پوسته توخالی ایجاد می کند و سپس نورد یا اکسترود شده و به اندازه لازم کشیده می شود. فرآیند تولید لوله بدون درز شامل مراحل اصلی زیر است.
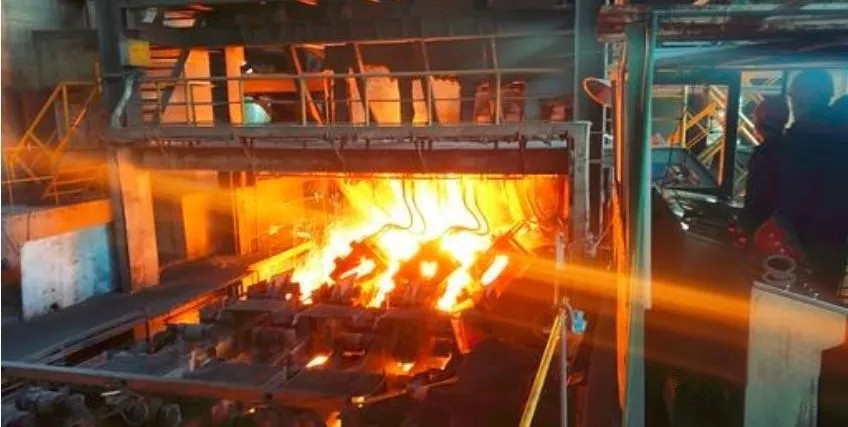
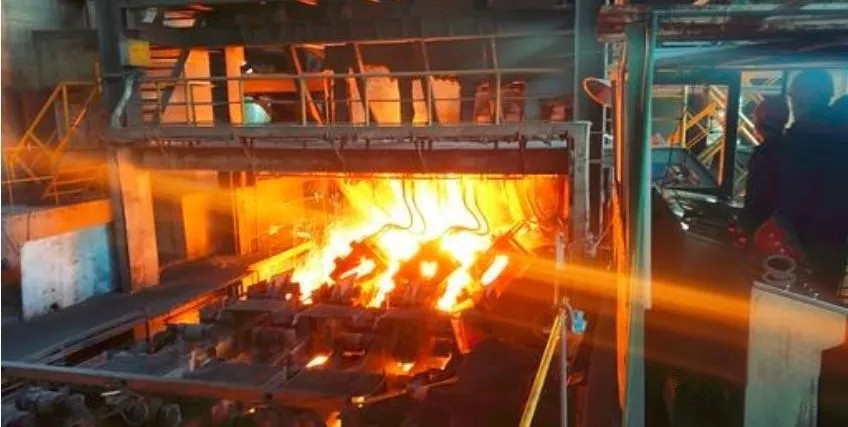
فرآیند تولید لوله های بدون درز (مانیسمان) چگونه است؟
ساختن روکش از لوله های توخالی با آسیاب یا اکسترود کردن
پانل لوله توخالی با کاهش قطر و ضخامت دیواره کشیده می شود
تولید لوله نهایی در فرآیند نورد سرد یا گرم
از آنجایی که معلوم می شود که این فرآیند تولید شامل جوش نیست، لوله بدون درز (Mannismann) قوی تر و قابل اطمینان تر می شود. لوله بدون درز نسبت به سایر انواع لوله در برابر فشار پایدار و بهتر است.
پس از پایان یافتن انحصار این فناوری، تغییرات مختلفی در فرآیند تولید به وجود آمد و مراحل شکلگیری آنها در فرآیندهای جدید ادغام شد. امروزه فرآیند تولید لوله به درجات مختلفی توسعه یافته است و این فرآیندها به فرآیندهای مدرن با کارایی بالا تبدیل شده اند.
بسته به اندازه لوله، ترکیب محصولات و همچنین در دسترس بودن مواد اولیه، تولیدات جدید لوله های بدون درز ساخته شد.
فرآیند نورد پیوسته و فرآیند سنگ زنی در محدوده اندازه گیری حدود 21 میلی متر تا 178 میلی متر قطر خارجی انجام می شود.
عملیات سنبه چند مرحله ای با سنبه معلق استوانه ای در اندازه های بین 140 میلی متر تا 406 میلی متر قطر خارجی، شمش را قادر می سازد از بیرون بسته شود.
فرآیندهای نورد و چرخش در اندازه های 250 تا 660 میلی متر وجود دارد. علاوه بر این، فرآیندهای جدیدی مانند آسیاب های ریسندگی، فرآیند Assel و Diescher یا اکستروژن لوله از پرس های Everhart توسعه یافتند. یک فرآیند معمولی تولید لوله بدون درز در شکل 1 نشان داده شده است.
فرآیند سنگ زنی و مهر زنی برای شکل دهی لوله
فرآیند سنگ زنی و سنگ زنی برای تشکیل لوله
شکل 1- فرآیند سنگ زنی و پانچ برای تولید لوله
تولید لوله های بدون درز
در این فرآیند شمش در کوره دوار تا دمای 1250 تا 1300 درجه سانتیگراد گرم می شود. قبل از کوره، شمش ها با فشار آب تمیز می شوند و به کارخانه سوراخ کردن سنبه منتقل می شوند و در آنجا شمش های سوراخ دار و پوسته های توخالی با دیواره ضخیم تولید می کنند.
در این فرآیند، ماده اولیه اولیه 1.5-2 برابر افزایش یافته و سطح مقطع 33-50 درصد کاهش می یابد. دستگاه حفاری دارای دو آسیاب نورد است که مخصوص لوله کشی طراحی شده اند که در یک جهت چرخش کار می کنند.
محور حدود 3 تا 6 درجه از خط رول افقی است. فضای بین بلوک ها عموماً توسط بلوک پشتیبانی کنترل نشده در بالا و یاتاقان پشتیبانی در پایین محصور و بسته می شود. نقطه فرز که به عنوان ابزار داخلی عمل می کند در مرکز شکاف رول قرار دارد و توسط یک بلوک فشار خارجی از طریق هسته سنبه مانند ثابت می شود.
پس از حفاری، یک دیواره ضخیم خالی مجدداً در موقعیت پیستون سوراخ می شود تا تولید لوله تکمیل شود. ضریب ازدیاد طول در فرآیند تف جوشی بین 5 تا 10 است و با کاهش 80 تا 90 درصدی سطح مقطع همراه است.
خط پانچ شامل دو پانچ (که گاهی اوقات به دلیل فشار دادن به قالب شناخته می شود) به شکل مخروطی در اطراف پانچ است. غلتک ها با حرکت متقاطع مواد اولیه سازگار شده اند. دمای کار در اطراف قالب ها بین 200 تا 220 درجه است و دارای یک ورودی مخروطی شکل، یک استوانه و یک فلپ است که در یک محفظه بزرگتر برای آزاد کردن قطعه کار قرار داده شده است. فرآیند فورج قالب یک فرآیند تا کردن گام به گام است که با چرخش قطعه به جلو و عقب کار می کند.
پس از اتمام فرآیند پیستون یا پرس شکل دهی، لوله تمام شده از سنبه خارج می شود. قسمت توخالی پوسته برش نامیده می شود. پس از گرم شدن در کوره، لوله به اندازه مناسب در خط نورد کاهش می یابد. آسیاب نورد قطر خارجی دقیقی ایجاد می کند و تمرکز و چرخش لوله را افزایش می دهد.
معمولاً از سه مرحله با دو یا سه لایه دقت تشکیل شده است. بپیچید (روی قرار دادن چند پایه) جایی که هر برگ در یک زاویه نسبت به خط باد جلو قرار دارد.
در انقباض یا انبساط، قطر خارجی لوله تا حد زیادی کاهش می یابد و ضخامت دیواره کمی افزایش یا کاهش می یابد. بسته به نوع محصول، کارخانه ها دارای 5 تا 28 مرحله نورد هستند.
پس از ساخت نهایی، لولهها در بستر خنککننده تا دمای محیط خنک میشوند و پس از بررسی دقیق به بخش تکمیل انتقال داده میشوند و در آنجا فرآیندهایی مانند ماشینکاری نوک لوله، صاف کردن و آزمایش هیدرولیک انجام میشود.
برای لوله های با قطر بزرگ که مواد ورودی معمولاً یک شمش چند ضلعی است استفاده می شود. این شمش پس از گرم شدن در کوره دوار، ابتدا در قالب دایره ای با سنبه عمودی قرار می گیرد. شمش جامد توسط یک پانچ استوانه ای به حدود نصف قطر سوراخ فشرده می شود و پوسته ای توخالی با پایه بسته ایجاد می کند.
عملیات بعدی شامل کاهش ضخامت دیوار با درجه کمی از گسترش طول لوله نورد است. در طی این فرآیند، انتهای لوله سوراخ می شود. پس از آن پوسته توخالی شکل لوله را در خط ابزار شکل دهی می گیرد و سپس عملیات اندازه گیری و برش انجام می شود.
فرآیند ماشه را خاموش کنید یا فرآیند را بکشید.
فرآیند نورد پلاگین یا فرآیند کشیدن
فرآیند نورد پلاگین یا فرآیند کشیدن
فرآیند نورد توپی برای رول لوله های بدون درز در محدوده قطر 60 تا 406 میلی متر با ضخامت دیواره تقریباً 3 میلی متر تا 40 میلی متر و طول لوله های 12 تا 16 متر استفاده می شود. حفاری در یک مرحله انجام می شود تا یک پوسته توخالی با دیواره نازک تشکیل شود که 3 تا 4.5 برابر طول اولیه خود است. و درجه تغییر 65 تا 75 درصد است.
خط آسیاب دارای دو چرخ جلو است که در هر دو جهت حرکت می کند. محور عقربه موازی با خط عمودی است و از 6 تا 12 درجه به سمت افقی می رود. فاصله بین ردیف های کاری با استفاده از بستر حافظه بالا و پایین تنظیم می شود.
این کفش های راهنما به فرآیند کشیدن کمک می کنند و به عنوان پین های ثابت عمل می کنند تا یک پوسته توخالی نازک تولید شود. همانطور که محصول از درون قالب بیضوی عبور می کند، خط نورد را دنبال می کند و به سنبه اجازه می دهد تا به طور موثر به عنوان یک ابزار داخلی برای تشکیل لوله عمل کند.
به دلیل زاویه شیب نسبتاً زیاد رول و سرعت رول بیشتر، سرعت خروجی محصول بسیار بالاتر است. این برای افزایش عمر سنبه بسیار مهم است. برای لوله های با قطر بزرگ یک سنبه ثانویه (به نام اکستندر) قبل از اتصال توپی وجود دارد.
سنبه های جدید دارای یک بخش منفذی مخروطی با پین های کاری دو شیار هستند، زیرا هر یک با محصول ساخته شده زاویه تقریباً 30 درجه دارند. و 10-12 درجه مورب نسبت به افق هستند. فاصله دویدن توسط دو دیسک جانبی بسته می شود که آنها نیز متحرک هستند
یک فرآیند نورد مداوم
پس از برداشتن سنبه، لوله های نورد قبل از پردازش در خط اندازه گیری برای کاهش یا حذف یک رول دوباره گرم می شوند. آسیاب کششی که از نظر ساخت شبیه به آسیاب نورد پیوسته است، از دوازده آسیاب فونداسیون بلند تشکیل شده است.
تنش زدایی یک تکنیک منحصر به فرد است زیرا با حذف استفاده از بریس و نگهدارنده سنبه، ضخامت دیواره را کاهش می دهد و در عین حال قطر لوله را کاهش می دهد. نیروی کششی که لوله بین آن قرار می گیرد نه تنها به طور موثر ضخامت دیواره لوله را کاهش می دهد، بلکه کاهش قطر در هر مرحله را می توان سه برابر کرد.
در تصویر زیر 4 مرحله نورد و پانچ برای تشکیل پوسته پس از آسیاب را مشاهده می کنید، دقیقا پس از اتمام سنگ زنی در مرحله نورد، لوله شکل نهایی خود را خواهد داشت. کاملا دایره ای است.
فرآیند نورد پلاگین یا فرآیند کشیدن
روش جمع شدن و رشد برای دو لوله کوچک استفاده می شود. از آنجایی که پانچ، رول و برش لوله های کوچک مقرون به صرفه نیست، تولید لوله های داغ با قطر کمتر از 75 میلی متر مستلزم کاهش و گسترش عملکرد دستگاه های خاص است. این دستگاه معادل یک خط پیوسته است. این ترکیب دارای 8 تا 16 بخش با دو غلتک با ضربات بلند 305 اینچ است.
برای قطرهای حدود 140 میلی متر و بالاتر، اندازه گیری هایی برای اطمینان از اندازه یکنواخت و گرد بودن طول لوله انجام می شود. بنابراین، روش اندازه گیری تنها شامل دو یا سه پایه اندازه گیری روی لوله است که سوراخ آن کمی کوچکتر از لوله نورد است. در برخی موارد، مسلح کردن مجدد مورد نیاز است
در برخی موارد، نورد و چرخش با فرآیندهای معمولی جایگزین می شود، به عنوان مثال، نورد مداوم، به عنوان مثال، با 9 پایه نگهدارنده جداگانه از غلتک های کشیده شده طولانی. پس از اینکه قطعه توسط یک خط نورد کشیده شد، سنبه روانکاری که به طور قابل توجهی بزرگتر از میله رزوه دار است وارد می شود و هر دو از خط نورد عبور می کنند.
فرآیند نورد پیوسته شامل چندین گذر از بیلت ها از طریق یک سری رول های چرخان برای تشکیل یک خط نورد است. این نوع نورد یک پوسته توخالی حفر شده روی خط فرز را می کشد و از سنبه استفاده می کند تا به عنوان یک ابزار داخلی عمل کند تا شکل نهایی لوله را بدهد.
فرآیندهای جدید به جای سنبه های شناور آزاد مدل کنترل شده از فرآیند نورد کارخانه استفاده می کنند. مزیت این نوع فرآیند در واقع این است که برای ساخت سنبه به میله های کوتاه تر و کمتری نیاز است. این نوع فرآیند نورد پیوسته به عنوان خط تولید لوله چند ایستگاهی (MPM) نیز شناخته می شود.
mpm
خمش لوله چند مرحله ای (MPM) بخشی از فرآیند نورد گرم لوله های بدون درز از طریق یک ژاکت سوراخ شده است. این وسیله نورد معمولاً از 8 پایه دو بلوک عمیق ساخته می شود که با زاویه 90 درجه نسبت به یکدیگر نصب می شوند. مصالح ساختمانی بر روی سنبه سرد و روغن کاری شده سوار می شود و در قالب اول، جایی که نورد شروع می شود، فشرده می شود. سنبه به موازات فرآیند MPM با سرعت ثابت اجرا می شود. سپس لوله برش داده می شود، کالیبره می شود، آماده می شود و قبل از حمل و نقل بازرسی می شود.
با این روش می توان به حداکثر انبساط دست یافت. طول لوله تولیدی می تواند تا 30 متر باشد. اعوجاج و عدم گرد بودن می تواند کمتر از 10٪ باشد.
اگر تا زمانی که میله سنبه بیرون کشیده شود، از فرآیند نورد مداوم استفاده شود. دمای لوله به حدود 500 درجه سانتیگراد کاهش می یابد. لوله مجدداً در دمای 950 تا 980 درجه سانتیگراد گرم می شود و روی یک رول کاهنده کشیده می شود.
کاهش و کشش رول می تواند شامل هر تعداد رول بین 24 تا 28 کانال یا بیشتر باشد که همگی در قالب خطی به هم متصل شده اند. هر براکت دارای درایو یا موتورهای قابل تنظیم خاص خود است و با سه براکت کوچک تکمیل می شود که قطر را وارد می کند. سه کلتک با هم مسیری را ایجاد می کنند که از ایستگاهی به ایستگاه دیگر محو می شود.
در این سیم پیچی از ابزارهای داخلی استفاده نمی شود و سرعت رول ها از ورود تا انتهای رول به طور مداوم افزایش می یابد.
بسیاری از فرآیندهای دیگر برای نورد لوله بدون درز وجود دارد. این فرآیندها شامل فرآیند پرس، فرآیند پانچ و کشش، فرآیند اکستروژن لوله و فرآیندهای نورد متقاطع است. فرآیندهای نورد متقاطع شامل فرآیندهای نورد مارپیچی و فرآیندهای نورد فرم است. علاوه بر این، لوله های بدون درز نیز با فرآیند شکل دهی سرد، کشش سرد و فرآیند نورد سرد تولید می شوند. در تصویر بالا طرح کلی و نمای کلی از فرز و نورد برای تشکیل پوسته توخالی را می بینید که برای رسیدن به قطر مورد نظر کشیده شده است.