ریخته گری فرآیند تشکیل فلزات و آلیاژها از طریق ذوب شدن، ریختن مذاب در ظرفی به نام قالب و سپس انجماد و سرد کردن آن برای مطابقت با شکل ظرف قالب است. این روش قدیمی ترین روش شناخته شده برای به دست آوردن شکل فلز مورد نظر است. اولین کوره های ذوب از خاک رس بود و لایه های مس و چوب یکی پس از دیگری روی هم چیده می شدند.
چدن
درصد بسیار بالایی از محصولات تولیدی حاوی حداقل یک محصول ریخته گری هستند. اندازه قطعات ریخته گری می تواند از چند گرم یا چند میلی متر (مانند تک دندانه های یک زیپ) تا 10 متر یا چندین تن (مانند یک ملخ بزرگ یا قاب کناری یک کشتی اقیانوس) متغیر باشد. فرآیندهای ریخته گری اغلب زمانی استفاده می شود که اشکال پیچیده یا قطعات توخالی یا قطعات با حفره های داخلی درگیر باشد. همچنین، قطعات با سطوح منحنی نامنظم (به غیر از ورق فلزی نازک)، قطعات بزرگ یا قطعات ساخته شده از فلزات که ماشین کاری آنها دشوار است، اغلب با ریخته گری تولید می شوند.
در اکثر روش های ریخته گری از الگو برای شکل دادن به قالب و ایجاد سوراخ در آن به شکل مورد مورد نظر استفاده می شود. قالب های قابل استفاده مجدد معمولا از چوب، پلاستیک یا فلز و قالب های یکبار مصرف معمولا از موم، پلاستیک یا فوم پلی استایرن ساخته می شوند. همچنین معمولاً از عضله یا هسته برای ایجاد فضاهای داخلی قطعات استفاده می شود.
ریخته گری 7 هزار سال. یافت شده در بین النهرین قبل از میلاد قورباغه مسی 3200 ساله قدیمی ترین قورباغه در جهان است.
به عبارت ساده، ریخته گری کارخانه ای است که با ذوب فلزات، ریختن فلز مایع در قالب و اجازه دادن به جامد شدن آن، قطعات ریخته گری را تولید می کند. ریختهگریها نه تنها محصولات فلزی را برای موتورها، ریلها یا قطعات لوله تولید میکنند، بلکه قطعاتی برای ماشینآلات مورد نیاز برای تولید بسیاری از محصولات مصرفی حیاتی هستند که ما به آنها وابسته هستیم.
تاریخچه بازیگری و روند
ریخته گری یک تکنیک ماقبل تاریخ است. دقیقاً مشخص نیست که چه زمانی ریختهگری فلز آغاز شد، اما در مطالعات باستانشناسی نسبتاً دیر ظاهر شد. باستان شناسان زمانی را که برای اولین بار در استفاده از فلزات تسلط یافتند، عصر پارینه سنگی می نامند که درست قبل از عصر برنز آغاز شد و گمان می رود بین 5000 تا 3000 سال قبل از میلاد باشد.
دهه 1800 شاهد پیشرفت های چشمگیری در فناوری ریخته گری بود. در سال 1889، با به رسمیت شناختن استفاده از نیکل برای افزایش استحکام فولاد، علم متالورژی نیز شروع به شهرت کرد. در سال 1809، ریخته گری گریز از مرکز A.G. توسعه یافته توسط اکهارت از انگلستان. ریخته گری گریز از مرکز به زودی توسط کارخانه های ریخته گری لوله پذیرفته شد و اولین بار در سال 1848 در بالتیمور مریلند مورد استفاده قرار گرفت. سر هنری بسمر از ریختهگری گریز از مرکز برای تصفیه گازها استفاده کرد و اولین کسی بود که دو یا چند فلز را در یک قالب چرخان ریخت. ریخته گری سانتریفیوژ فولاد برای اولین بار در سال 1898 در کارخانه فولاد آمریکا در سن پترزبورگ انجام شد. در سال 1901، چرخ های واگن قطار با سرعت 620 دور در دقیقه می چرخید
پس از معرفی فرآیند گریز از مرکز، فرآیند ساخت قالب پیوسته به نام ریختهگری لجن معرفی شد. ماشینهای دایکست دستی در سال 1849 (Sturgis) و 1852 (Barr) ثبت اختراع شدند]
یکی از قدیمی ترین روش های ریخته گری، موم قربانی نیز در سال 1897 توسط B.F. فیلبروک از آیووا بهبود یافت. صنعت به این فرآیند پیچیده توجهی نکرد تا اینکه نیازهای نظامی سنگین جنگ جهانی اول مجبور به تولید ماشین ابزار شد. سپس برای تولید قطعات کامل و دقیق، بدون استفاده از زمان، جوشکاری و مونتاژ، میانبرهایی مورد نیاز است. تلاشهای دیگر در این زمان شامل ساخت اولین کارخانه تولید مسلسل در ایالات متحده (یکی از اولینها در جهان)، کارخانهای در راکفورد، ایلینوی بود که در سال 1918 نارنجکهای دستی برای ارتش ایالات متحده تولید میکرد
اولین جداسازی آلومینیوم در سال 1825 اتفاق افتاد، اما کاربردهای مهندسی قابل توجهی تا اواخر قرن 19 رخ نداد، زمانی که هزینه آلومینیوم به دلیل بهبود فرآیندهای ذوب و بهبود فرآیندهای کاری کاهش یافت.
توسعه قرن بیستم
فن آوری ریخته گری در قرن بیستم به جهات مختلفی پیشرفت کرده است، میزان این پیشرفت ها از زمان جنگ جهانی دوم بیشتر از پیشرفت در همه صنایع در مجموع در 3000 سال گذشته است. برای بیش از 400 سال، فرآیند ریخته گری و مواد اغلب بر اساس روشی است که توسط “پدر ریخته گری” در قرن 16th Venocchio Bringusio، که استفاده از لجن مرطوب آبجو و ادرار انسان را به عنوان چسب برای قالب گیری شن و ماسه توصیه می کرد، توسعه داده شد. این روشها و دستورالعملها تا قرن بیستم مورد استفاده قرار میگرفت. تا دهه 1920، آزمایش شن و ماسه فقط شامل فشردن مقدار کمی شن برای تعیین توانایی آن در فشردهسازی و نگهداشتن آن بود. در آغاز همان دوره، تیم تحقیقاتی انجمن بنیانگذاران آمریکا شروع به توسعه روش هایی برای آزمایش شن و ماسه کرد. در سال 1924 استانداردهایی تهیه شد که خواص مختلف ماسه قالب گیری را پوشش می دهد.
پس از جنگ جهانی دوم، آزمایشها با ماسههای آلی و شیمیایی برای قالبها و قالبهای ترموست نیز تشدید شد. با شروع فرآیند تاج گذاری (فرایند پوشش)، ابتدا از فنل ها استفاده شد، سپس از اوره و فرآیند دی الکتریک به عنوان چسب استفاده شد و سپس فوران ها و رزین های بدون اوره جایگزین شدند. توسعه مداوم چسبها برای تولید قالبهای ماهیچهای و با پیوند شیمیایی منجر به افزایش بهرهوری و همچنین دستیابی به تکرارپذیری ابعادی لازم برای برآورده کردن الزامات جدید برای قالبهای تمیز و تقریباً تمیز برای ریختهگری میشود.
ریخته گری فرآیند ذوب قالب به شکل محفظه است، بنابراین تولید اشکال پیچیده تنها با روش های ریخته گری امکان پذیر است، زیرا مذاب می تواند با ریختن در قالب شکل قالب را به خود بگیرد. اگر روش های شکل دهی حالت جامد باشند، به دست آوردن اشکال پیچیده دشوار است. در این دایره المعارف می خواهیم با روش های مختلف ریخته گری فلزات آشنا شویم. انواع روش ها:
ریخته گری شن و ماسه
دقیقا
تزریق گریز از مرکز
مجموعه فروشگاه آهن قیمت بیلت را در حالت ها، استانداردها، ابعاد و طول های مختلف ارائه می دهد. برای اطلاع از قیمت ها به لیست قیمت مربوطه مراجعه فرمایید.
ریخته گری در شن و ماسه
این نوع روش آسان است. در این روش ابتدا فلز یا آلیاژ را کمی بالاتر از دمای ذوب آهن در یک بوته سرامیکی حرارت می دهیم. سپس مذاب را برای قوام در یک لوله شیشه ای که در تماس با مذاب ذوب نمی شود، هم می زنیم. مذاب را داخل قالب می ریزیم و به قطعات زمان می دهیم تا سفت شوند. بعد از یخ زدن کامل قالب ها را باز می کنیم و ماسه ها را پاک می کنیم. درب و سیستم تغذیه باید بلافاصله با یک ضربه برداشته شود. در مرحله بعد، گاهی برای رسیدن به خواص مکانیکی بهتر، قطعه را گرم می کنیم.
معایب ریخته گری معمولی (ریخته گری شنی):
محدودیت ها در به دست آوردن خواص مکانیکی نهایی بسیار مهم هستند، به همین دلیل، برای به دست آوردن کیفیت بهتر، قطعات ریخته گری اغلب عملیات حرارتی می شوند.
کیفیت و یکنواختی سطح در بسیاری از این فرآیندها، به ویژه در ماسه، ضعیف است و نیاز به کار ثانویه دارد.
تماس مستقیم کارگر با مذاب نشان دهنده خطری برای جان کارگر است.
مشکلات زیست محیطی و آلودگی
انداختن تو شن
ریخته گری دقیق برای ریخته گری سرمایه گذاری
روش دقیق یا همان روش (Casting Deposit) که با نام Lost-Wax نیز شناخته می شود، روشی است که در آن قالب ها از مواد فراری تهیه می شود که پس از اتمام انجماد از بین رفته و در اثر حرارت حاصل از ذوب، آنها را تهیه می کنند. آماده می شوند. با. روش های ماست سرامیکی و به دلیل فرار بودن آن ها می توان گفت که هم مدل ها و هم قالب ها فقط یک بار به صورت خاص استفاده می شوند.
با توجه به نوع آماده سازی قالب دو روش مختلف وجود دارد:
روش پوسته
روش تاپر
به طور کلی می توان گفت که این دو روش در ساخت مدل تفاوتی ندارند و تنها در نوع قالب با هم تفاوت دارند.
مهمترین مزیت در ریخته گری دقیق
به لطف دقت ابعادی این روش، امکان طراحی و ریخته گری قطعات پیچیده صنعتی وجود دارد.
امکان به دست آوردن انواع فولاد و آلیاژهای فولادی.
اندازه بسیار سازگار مطابق با استانداردهای ASM.
کیفیت سطح بالاتر از کیفیت سطح قطعات تولید شده توسط سندبلاست می باشد.
کاهش سطوح برش به لطف کیفیت سطح بهتر و در نتیجه صرفه جویی در ضایعات مواد.
با پیش گرم کردن یا بازپخت کردن قالب های سرامیکی قبل از این فرآیند، عیوب را به حداقل برسانید و احتمال ترک های سطحی را کاهش دهید.
به دلیل نقص کمتر در فرآیند ریخته گری می توان به خواص مکانیکی بالاتر دست یافت.
به دلیل فرار بودن مواد قالب گیری، خط جداکننده حذف می شود و با حذف این خط، عیوب ناشی از خط جداکننده برطرف می شود.
محدودیت های مهم ریخته گری استاندارد
اندازه و وزن قطعات تولید شده به این روش محدود است و عموما قطعات با وزن کمتر از 5 کیلوگرم به این روش تولید می شوند.
هزینه تجهیزات و ابزار در این روش نسبت به سایر روش ها بیشتر است.
ریخته گری به روش ریخته گری
این ریخته گری یکی از روش های دائمی است که در آن آلیاژ تحت فشار زیاد وارد محفظه قالب می شود. روش دائمی به روش هایی اطلاق می شود که برای قطعات متوالی استفاده می شود که قالب را از بین نمی برد. این قالب ها از فلز ساخته شده اند. در این روش مایعی که تحت فشار به قالب فرستاده می شود، تا زمانی که در نهایت جامد شود، تحت فشار می ماند و پس از انجماد کامل می شود. فشار آزاد می شود، قالب باز می شود و قطعه خارج می شود. فشار مورد استفاده در این روش بین 7 تا 35 مگاپاسکال است.
مزایای ریخته گری می میرد
به دلیل صرفه جویی در فرم، برای تولید در مقیاس بزرگ مناسب است.
دقت ابعادی (±0760) و کیفیت سطح خوب است.
امکان تولید قطعات نازک وجود دارد.
به دلیل سرعت خنک کنندگی بالا، ریزساختار و خواص مکانیکی بهبود یافته است.
معایب دایکست
به دلیل محتوای فولادی قالب، این روش عموماً به فلزات با نقطه ذوب پایین محدود می شود و امکان تولید قطعات بسیار پیچیده وجود ندارد.
وجود صفحات در محلول و سوزن فنری
ریخته گری گریز از مرکز
در این روش ریخته گری نیرویی که باعث ورود فلز مذاب به داخل قالب می شود نیروی گریز از مرکز است که باعث توزیع مذاب روی بدنه قالب می شود، این نیرو با چرخش سریع قالب ایجاد می شود.
ریخته گری گریز از مرکز A Reba ya ریخته گری گریز از مرکز
این روش به سه روش انجام می شود:
یک عجیب و غریب واقعی
نیمه گریز از مرکز
تحت نیروی گریز از مرکز یا مقاطع گریز از مرکز
معایب این روش را می توان به صورت زیر خلاصه کرد.
پر بودن قطعه به دلایل زیر مرتبط است: آب ذوب کم، دمای فوق ذوب پایین، سرعت پایین ریختن مذاب در قالب و ورود قسمت کوچکی از مذاب از این طریق.
ترک سرد زمانی رخ می دهد که دو جبهه جریان مذاب در هنگام رسیدن به یکدیگر به دلیل سرد شدن زود هنگام به یکدیگر نفوذ نکرده و باعث ایجاد ترک در داخل قطعه می شود.
پنینگ سرد به پاشیدن فلز مذاب در حین ریخته گری و تشکیل دانه های جامد و محفظه در قطعه اشاره دارد.
ایجاد حفره های انقباضی که همانطور که از نامش پیداست فرورفتگی های سطحی یا حفره های داخلی ناشی از جمع شدگی پس از انجماد هستند.
قطعات در ماشین آلات و تجهیزات با استفاده از فرآیندهای ساخت تولید می شوند. برخی از این قطعات در مقیاس کوچک و برخی در مقیاس بزرگ و صنعتی تولید می شوند. یکی از رایج ترین روش های ساخت، ریخته گری است. ریخته گری یک فرآیند پرکاربرد برای ساخت قطعات فلزی است. این فرآیند در صنایع خودروسازی و مکانیکی بسیار محبوب است. در این مقاله به معرفی اصول و مفاهیم ریخته گری می پردازیم. در ابتدا به بررسی کاربردها، مواد مورد استفاده، انواع روش های پیاده سازی، روند کلی پیاده سازی، مزایا، معایب و معایب این سیستم می پردازیم. در مرحله بعد، تاریخچه، اصطلاحات رایج و انواع تکنیک های ریخته گری را بررسی می کنیم. در نهایت نکات و منابع تکمیلی را برای مطالعه این برنامه مهم ارائه خواهیم کرد.
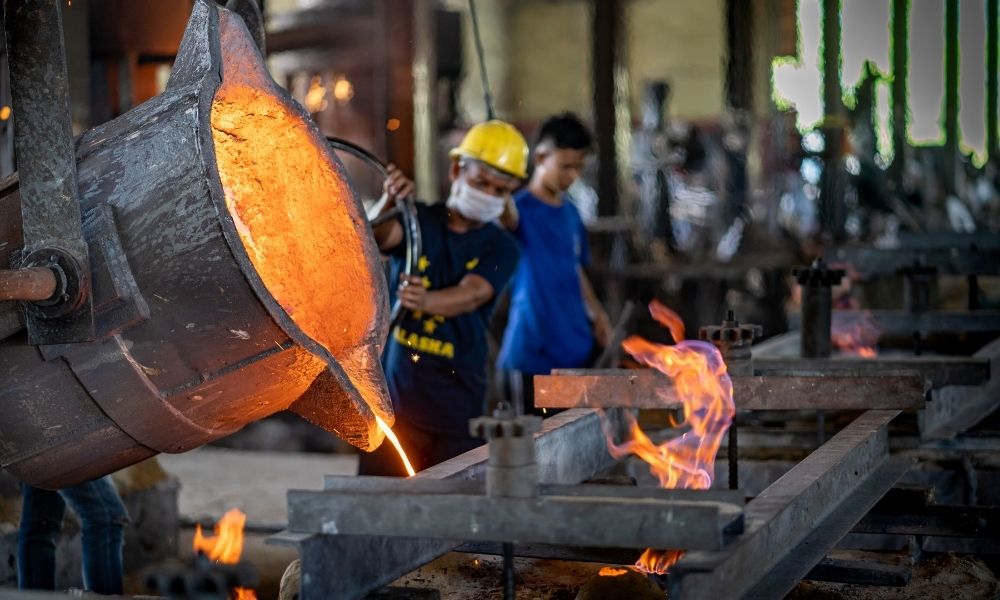
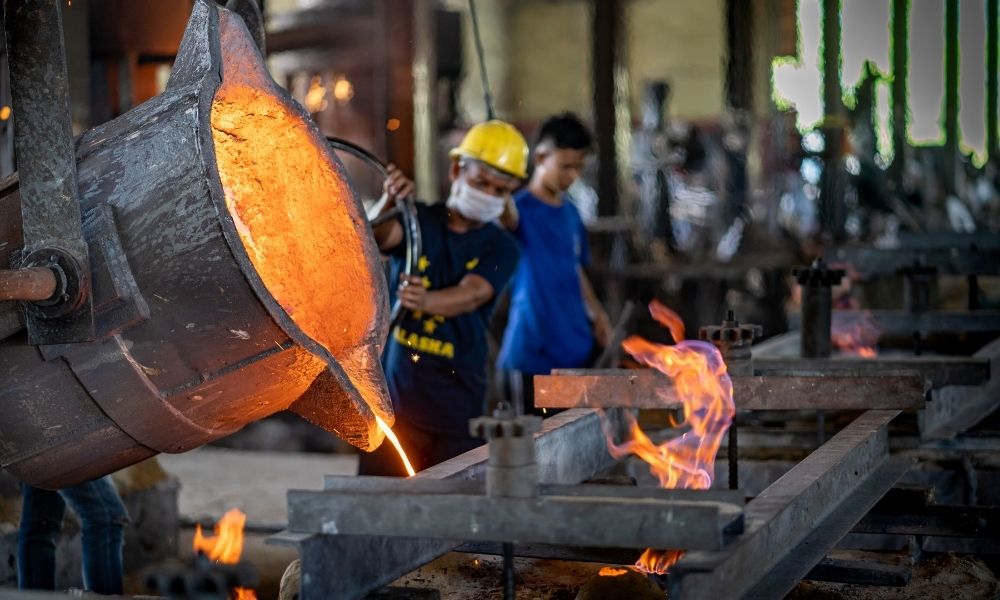
ریخته گری چیست؟ انواع و روش های مختلف و کاربرد ها
روش های تولید چیست؟
تولید یک اصطلاح کلی است که به مجموعه فعالیت های مورد نیاز برای ساختن بخشی در صنایع مختلف اشاره دارد. روش ها و فرآیندهای مختلفی برای ساخت قطعات صنعتی و غیر صنعتی وجود دارد. به عنوان مثال، قطعات پلاستیکی مورد استفاده در بسیاری از لوازم خانگی با استفاده از روش قالب گیری تزریقی تولید می شوند.
در فرآیند قالب گیری تزریقی تعدادی قطعه ساخته می شود
مجموعه ای از قطعات ساخته شده به روش قالب گیری تزریقی
شناخته شده ترین روش های تولید عبارتند از:
به بازیگران
پوشش و حکاکی: حکاکی لیزری، چاپ، رسوب بخار شیمیایی، کندوپاش، آبکاری، پاشش حرارتی
قالب گیری: پودر فلز، قالب گیری پلاستیک و پوشش کوچک
ساخت: تکمیل لوله، شکل دهی، نورد، اکستروژن، پرس، خمش، برش و غیره.
پاشش: فرز، تراشکاری، حفاری، تزئین، برش لیزری، جت آب، برش پلاسما، تخلیه الکتریکی، اره و غیره.
اتصال: جوشکاری، فلز، لحیم کاری، چسب، پیچ و غیره.
تولید افزودنی: چاپ سه بعدی، حکاکی لیزری، سیال پیچشی، فیلامنت ذوب شده، لایه بندی، برش پلاسما، استریوگرافی و غیره.
روش های دیگر: معدن، تولید مواد شیمیایی، پتروشیمی، مونتاژ، لجستیک، بسته بندی، نجاری، عملیات حرارتی (مانند سخت کاری)، پخت و غیره.
از مواد فوق برای ساخت و ساخت فلزات، پلاستیک، پلیمرها و غیره استفاده می شود. فرآیندهای تولید می تواند خاص (شرکت ها و محصولات خاص) یا عمومی باشد. بله، توجه داشته باشید که می توان فرآیندهای تولید را به چند گروه تقسیم کرد. به عنوان مثال، ریختهگری، شکلدهی و اتصال از فرآیندهای فلزکاری در نظر گرفته میشوند.
ریخته گری چیست؟
“ریخته گری کامل” یک فرآیند صنعتی قدیمی است که شامل ذوب مواد و ریختن آنها در قالب است. این فرآیند یکی از روش هایی است که برای ساخت قطعات فلزی در صنایع مختلف مورد استفاده قرار می گیرد. ریخته گری امکان تولید انبوه قطعات از اندازه های کوچک تا بزرگ، مقیاس از چند گرم تا چندین تن، اشکال ساده تا پیچیده و سیستم های یکپارچه را فراهم می کند. راه های زیادی برای برش وجود دارد. با این حال، ریخته گری شن و ماسه به عنوان قدیمی ترین و رایج ترین روش ساخت بتن شناخته می شود.
مواد مذاب را در قالب های ماسه ای بریزید
مخلوط را در قالب ماسه ای بریزید.
برنامه ریخته گری چیست؟
ریخته گری تقریبا در تمام صنایع استفاده می شود. حدود 90 درصد محصولات تولید شده در صنایع مختلف و ماشین آلات صنعتی به نوعی با فرآیندهای ریخته گری مرتبط هستند. با این حال، بیش از 50 درصد قطعات ریخته گری در ماشین آلات سنگین و صنعت تجهیزات حمل و نقل استفاده می شود.
الگوهای ریخته گری مورد استفاده در اتومبیل
نمونه هایی از ریخته گری های مورد استفاده در اتومبیل
صنایع و زمینه های مختلف که در آن راه حل ها استفاده می شود عبارتند از:
حمل و نقل: تولید خودرو؛ تجهیزات راه آهن؛ تجهیزات راه آهن و کشتی سازی
تجهیزات سنگین: راهسازی، تجهیزات کشاورزی و معدن
ماشین آلات: ماشینکاری، قالب گیری تزریقی، آهنگری، اکستروژن، قالب گیری و تجهیزات ریخته گری
ماشین آلات صنعتی: تجهیزات شیمی، شیمی، کاغذ، شکر، منسوجات، ذوب و تولید برق.
صنایع نظامی: وسایل نقلیه، سلاح، مهمات، تانک و تجهیزات تعمیر و نگهداری
صنایع برق: موتور، ژنراتور، پمپ و کمپرسور
تاسیسات: لوله ها، اتصالات، شیرها و اتصالات مورد استفاده در خطوط لوله، تاسیسات بهداشتی و تاسیسات تبرید.
لوازم خانگی: لوازم آشپزخانه، مبلمان، تجهیزات باغبانی
هنر: مجسمه سازی، زیور آلات، تزئینات و غیره
چه موادی برای ریخته گری استفاده می شود؟
چدن خاکستری پرکاربردترین ماده در فرآیند ریخته گری است. سایر فلزات رایج در این فرآیند عبارتند از چدن، آلومینیوم، فولاد، مس و روی. البته برای ساخت قطعات ریخته گری می توان از مواد غیرفلزی مانند بتن، شیشه، پلاستیک و رزین استفاده کرد. انتخاب مواد مناسب برای ساخت قطعات به پارامترهایی مانند حجم تولید، بازده اقتصادی، دمای ذوب، سرعت خنکسازی، مقاومت در برابر سایش، وزن و توانایی جذب ارتعاشات بستگی دارد. نوع ماده مورد استفاده یکی از معیارهای تفکیک انواع روش های ریخته گری و کاربرد آنها می باشد.
ذوب یا ریخته گری چیست؟
ریخته گری مکانی است که در آن قطعات فلزی با ریخته گری تولید می شود. تمام مراحل ریخته گری در این کار انجام می شود. از تجهیزات و مواد مورد استفاده در کارخانه های ذوب می توان به تجهیزات شکل دهی، میکسرها، کوره ها، بوته ها، تجهیزات حمل و نقل، فیلترها، فلزات، آلیاژها، مواد افزودنی و سیستم های پیوند شیمیایی اشاره کرد.