تقویت میلگرد در برابر خوردگی به جلوگیری از ریزش سازه های بتن مسلح و افزایش عمر سازه کمک می کند. خوردگی یا خوردگی میلگرد باعث ترک خوردگی میلگرد و کاهش شکل پذیری و چسبندگی با بتن و در نتیجه آسیب به سازه و کوتاه شدن عمر آن می شود. روش های جلوگیری از زنگ زدگی یا خوردگی میلگرد بسیار متفاوت و پرکاربرد است. اما مهم ترین روش ها و روش های اصلی استفاده از پوشش بتنی خوب و همچنین استفاده از انواع پوشش ها بر روی میلگرد می باشد. در این مقاله روش های مختلف جلوگیری و زدودن زنگ زدگی میلگرد و نحوه تعمیر یا تعویض میلگرد زنگ زده را به تفصیل بررسی می کنیم.
1 فرآیند خوردگی میلگردها
2 روش برای جلوگیری از خوردگی آرماتور در بتن
با محافظت از بتن از خوردگی میلگرد جلوگیری کنید
4 جلوگیری از خوردگی آرماتور با حفاظت مکانیکی آرماتور (پوشش محافظ روی سقف)
5 راه های ویژه دیگر برای جلوگیری از خوردگی میلگرد
6 راه برای مقابله با خوردگی میلگردهای انبار
7 نکته برای تقویت میلگرد در برابر خوردگی
8 راه برای از بین بردن خوردگی میلگرد
9 چگونه اتصالات زنگ زده در سازه را تعمیر یا تعویض کنیم؟
تقویت فرآیند خوردگی
به دلیل پوشش ناکافی روی میلگرد، لایه نازکی از اکسید روی سطح آن ایجاد می شود و در نهایت میلگرد از کار می افتد. اگر اقدامات لازم برای حفاظت از ساختمان انجام نشود، تغییر شکل فولاد باعث ایجاد ترک می شود و پوشش باعث از بین رفتن این مواد می شود که باعث استحکام بیشتر آن می شود. یکی از عواملی که باعث تغییر شکل و شکستگی سطح میلگرد می شود وجود یون های خورنده، آب، اکسیژن و عوامل محیطی است. برای آشنایی بیشتر با خوردگی میلگرد و انواع آن توصیه می کنیم مقاله زیر را مطالعه کنید.
# باید خوانده شود
آهن ملت
پیشنهاد کارشناسی Ahn Mills: بررسی انواع خوردگی آرماتورها در بتن
خوردگی تقویتی
برای جلوگیری از خوردگی آرماتور بتن باید راه حل هایی برای جلوگیری از ورود مواد خورنده به میلگرد و یا افزایش مقاومت شیمیایی آرماتور در برابر مواد خورنده در نظر گرفته شود. بنابراین، روش های مختلفی برای محافظت از بتن مسلح در برابر خوردگی وجود دارد. همه این روش ها در زیر بررسی می شوند.
روشهای جلوگیری از خوردگی آرماتورها در بتن
روش های جلوگیری از خوردگی میلگرد در بتن
موثرترین راه برای محافظت از میلگرد در برابر خوردگی ایجاد عمق مناسب پوشش بتن و در نتیجه جلوگیری از ورود یون های غیرفعال کننده مانند کلرید است. یکی دیگر از روش های موثر و پرکاربرد، تقویت میلگرد و پوشاندن میلگرد با مواد مناسب است. با استفاده از روش های جلوگیری از خوردگی میلگرد، مدت زمان رسیدن عناصر مخرب و خورنده به میلگردهای مدفون در بتن افزایش یافته و در نهایت دوام سازه به میزان قابل توجهی افزایش می یابد.
در ادامه 12 راه برای جلوگیری از خوردگی میلگرد ارائه می کنیم. در تمامی این روش ها هدف اصلی جلوگیری از واکنش بین یون کلرید و میلگرد میلگرد و در نهایت جلوگیری از خوردگی می باشد.
جلوگیری از ساپورت خوردگی با حفاظت
جلوگیری از فرسایش مجدد با محافظت از بتن
1- بهبود عملکرد پایدار
اولین و موثرترین راه برای جلوگیری از خوردگی ایجاد یک پوشش بتنی مناسب روی نرده است. صرف نظر از روش دیگر جلوگیری و تاخیر در خوردگی میلگرد، ابتدا باید ساخت و اجرای بهترین بتن انجام شود. به دلیل استفاده از مخلوط آب و سیمان به مقدار مناسب و سیمان کافی که استفاده از یون کلر و کربناته شدن را تا حد زیادی به تاخیر می اندازد.
همچنین مواد افزودنی جایگزین سیمان و موادی مانند سرباره، خاکستر بادی، دود سیلیس و سایر مواد باعث کوچک شدن یا بسته شدن حفره های موجود در بتن می شوند. در نتیجه از خوردگی پشت جلوگیری کرده و پایداری بتن را افزایش می دهند.
2- استفاده از پوشش بتنی.
همانطور که قبلاً گفتیم، قرارگیری صحیح بتن اولین راه برای محافظت از میلگرد در برابر خوردگی است. اما انواع شیشه ای بتن نیز وجود دارد که به بتن در جلوگیری از خوردگی میلگرد کمک می کند. به طور کلی به پوشش بتنی اطراف تیرک ها روکش یا پوشش بتنی می گویند. در قوانین، پوشش بتنی به شرح زیر تعریف شده است: “حداقل فاصله از بالای آرماتور هم از نظر طول و هم در نهایت در ناحیه مستقیم بتن”.
پوشش بتنی از فولاد در برابر عناصر طبیعی، اکسیداسیون، اثرات شیمیایی، ورود یون های کلرید، رطوبت محافظت می کند و در نتیجه از خوردگی جلوگیری می کند.
انواع روکش های بتنی
حفاظت از سطح بتن و نوع پوشش بستگی به عوامل زیادی مانند مقاومت در برابر نفوذ آب، مقاومت در برابر دی اکسید کربن، یون های کلرید، عوامل شیمیایی، سهولت اجرا دارد.
پوشش
به طور کلی انواع پوشش بتن یا حفاظ سطح بتن را می توان به سه دسته زیر تقسیم کرد:
پوشش های سطحی (گچ)
مسدود کننده های منافذ
نفوذ پذیری
1- پرداخت سطحی (نسخه ها)
پوشش سطحی به صورت یک لایه نسبتاً ضخیم ملات سیمان اجرا می شود و معمولاً با کمک ماله مناسب روی سطح اصلی بتن پخش می شود. ملات سیمان نمی تواند حاوی مواد پلیمری باشد. اما در بیشتر موارد با مواد پلیمری (لاتکس) اصلاح می شود. استفاده از مواد پلیمری باعث کاهش نفوذپذیری بتن در برابر عوامل خورنده می شود.
محبوب ترین انواع پوشش عبارتند از:
اپوکسی (محلول در آب یا محلول در آب)
پلی استر
اکریلیک
پلی اورتان
اما روزها
قیر و آسفالت
2- محدودیت های پشتیبانی
پرکننده های منافذ موادی هستند که وارد منافذ و منافذ ریز بتن و خمیر سیمان می شوند. در این حالت یا منافذ بتن به طور کامل پر می شود یا این مواد با اجزای خمیر سیمان (مانند آهک) واکنش داده و ماده ای نامحلول، چسبناک و پر شده را تشکیل می دهند. برای استفاده از این سطح بتنی، سطح باید تمیز و عاری از روغن و گرد و غبار باشد. اما لازم نیست بتن سخت باشد. پرکننده های مو ممکن است شامل سیلیکات سدیم یا سیلیکو فلوریت باشد که به صورت محلولی در آب داغ روی سطح اسپری می شود.
3- مقدمه
موادی که حالت مایع و ویسکوزیته پایین دارند، نافذ نامیده می شوند. مواد نافذ بر روی سطح بتن پاشیده یا مالیده می شوند تا در منافذ و سوراخ های کوچک بتن نفوذ کند، اما سوراخ ها را پر نکند. بلکه با تغییر جهت کشش سطحی، سوراخ های مویین رطوبت را از داخل به بیرون می راند، بنابراین رطوبت و گازهای مضر دیگر نمی توانند وارد بتن شوند (مانند شیر یک طرفه). مواد نافذ برای تصفیه آب طولانی مدت چندان مناسب نیستند و بیشتر برای استفاده در سطوح بتنی که به طور مرتب در معرض آب قرار نمی گیرند مناسب هستند. شناخته شده ترین مواد نافذ سیلان ها و سیلوکسان ها هستند.
3- پوشش بتنی (پوشش های ضد آب)
از آنجایی که بتن یک ماده متخلخل و نفوذپذیر است، آب بندی بتن یک راه حل اساسی و مهم برای محافظت از سازه های بتنی است که در تماس دائمی یا غیر دائمی با آب یا مواد شیمیایی هستند. اگرچه بتن از مقاومت و استحکام بالایی برخوردار است، اما به دلیل اجزای تشکیل دهنده (سندانه، ماسه، سیمان و آب) معمولاً در برابر آب و مواد شیمیایی بسیار مقاوم است. به همین دلیل اگر بتن را آب بندی نکنیم، آب، رطوبت و کثیفی محیط را به خود جذب می کند و علاوه بر تضعیف و فرسایش بتن، باعث خوردگی و فرسودگی بتن می شود.
انواع روش های مهر زنی بتن عبارتند از:
صفحه ضد آب (صفحه غشایی)
مهر و موم دیافراگم مایع
محلول ضد آب فوری
ملات ضد آب دو جزئی
پوشش پودری پلیمری
آب بندی با چسب بتن (چسب سقفی)
سقف سیمانی
افزودنی های فناوری نانو
رزین پلی اورتان
در بین روش های فوق استفاده از پنل های ضد آب مفید و موثرتر است. به همین دلیل ما جداگانه بررسی می کنیم.
صفحه آب بندی
صفحات مهر و موم شده
سیستم صفحه غشایی یکی از محصولات اصلی برای آب بندی بتن می باشد. دلیل این امر تاثیر خوب این مواد بر استحکام، سختی و دوام بتن و جلوگیری از نفوذ آب و کلرید و در نتیجه جلوگیری از خوردگی میلگرد می باشد. صفحات غشایی را می توان به دو صورت جامد و مایع (عایق امولسیونی) استفاده کرد.
یکی از مزایای استفاده از ورق های غشایی جامد، خودچسب بودن و حذف مواد مضر از چسب آسفالت ورق است که باعث سازگاری بیشتر این محصول با محیط زیست و سهولت در استفاده می شود. در عین حال این دال ها باعث افزایش مقاومت بتن و مقاومت در برابر خاک های اسیدی می شود. اما یکی از بزرگترین مشکلات این محصول نصب صحیح و مبتنی بر قوانین آن است. زیرا در گوشه ها، کناره ها و بین دو تخته باید به درستی چیده و تراز شود. ضمناً صفحات نباید دارای سوراخ و سوراخ بوده و کاملاً جامد باشند.
عایق ضد آب غشایی مایع یا امولسیونی نیز با استفاده از برس، سمپاش، غلتک و ماله اعمال می شود. یکی از مشکلات این محصول تماس غشای مایع با اشعه UV است. در این صورت این محصول دیگر تحمل بار پیاده روی و ترافیک را ندارد.
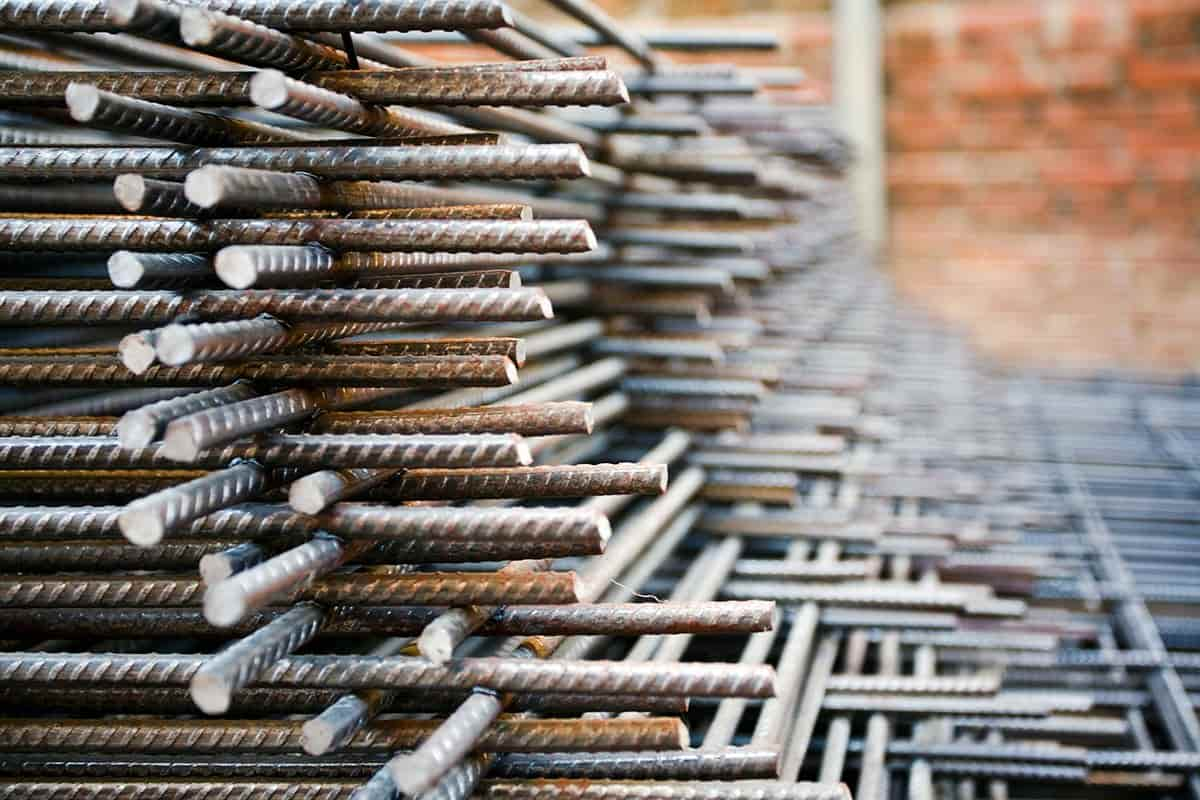
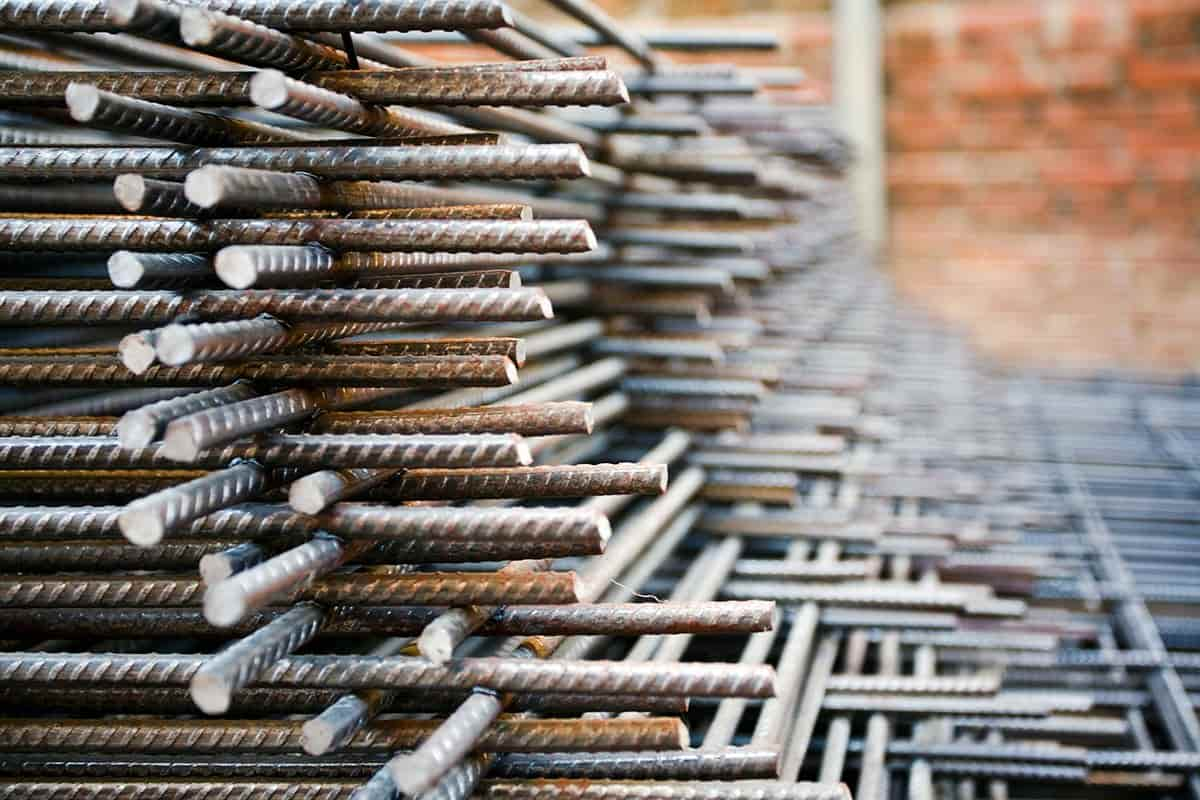
راهنمای جامع محافظت و تقویت میلگرد در برابر خوردگی
4- استفاده از بازدارنده های خوردگی
بازدارنده اولیه خوردگی که بیشتر با بتن سازگار است نیترات کلسیم است. نیترات کلسیم نوعی تسریع کننده گیرش و سفت شدن بتن است و خاصیت گیرش سریع یا ضد یخ را در بتن ایجاد می کند. این مواد را می توان بدون تأثیر بر طراحی، ساخت یا عملکرد بتن به مخلوط بتن اضافه کرد. این امر زمان عمل آوری بتن را از 12 ساعت به 4-5 ساعت کاهش می دهد. به طور کلی، از آنجایی که حاوی یون کلر نیست، نیترات کلسیم مایع برای استفاده به عنوان یک بازدارنده خوردگی در فولاد مناسب است.
جلوگیری از خوردگی بست به دلیل حفاظت مکانیکی آرماتور (پوشش محافظ روی بست ها)
جلوگیری از خوردگی آرماتور با حفاظت مکانیکی آرماتور
جداسازی آرماتور از محیط و عایق بندی آن در برابر تماس با عوامل خورنده (هوا، رطوبت و یون کلر) راه دیگری برای جلوگیری از خوردگی آرماتور و افزایش دوام بتن مسلح است. اگر مواد مضر بخصوص یون کلر بتوانند از پوشش بتن روی آرماتور نفوذ کنند، آرماتور زنگ می زند. به همین دلیل، یک پوشش محافظ روی میله تقویت کننده اعمال می شود.
تجربه نشان داده است که زمان رسیدن یون های کلر به میله های تقویت کننده تابعی از نیروی جرم است. یعنی اگر مثلاً ضخامت روکش روی میله دو برابر شود زمان شروع پوسیدگی دو برابر می شود. روش های مختلفی برای ساخت عرشه میلگرد ارائه شده است که اغلب با بسیاری از شرایط مشابه. مهمترین آنها شامل موارد زیر است:
5- پوشش قلیایی-اسیدی اتصالات
فرآیند برش و خم کردن میلگرد و سپس استفاده از مواد اسیدی و قلیایی برای تقویت میلگرد در محل ایزوله برای ایجاد خواص ضد خوردگی. در عمل میلگردها بر روی تکیه گاه های چوبی یا بنایی در محیط ایزوله قرار می گیرند و تقریباً. یک لایه محافظ 0.1 میلی متری روی آنها قرار می گیرد.
فرآیند تقویت آرماتورها برای حفاظت در برابر خوردگی با استفاده از مواد اسیدی و قلیایی به شرح زیر خلاصه می شود:
میلگردهای تقویت کننده تقریباً 15 تا 30 دقیقه در محلول آنتی اکسیدانی غوطه ور می شوند تا خوردگی را از بین برده و سطح را جلا دهند. محلول آنتی اکسیدانی با مخلوط کردن محلول بازدارنده با اسید هیدروکلریک و آب تهیه می شود. مخلوط متوسط موجود در این محلول 5 لیتر آنتی اکسیدان و 50 لیتر اسید کلریدریک است و برای تولید 100 لیتر محلول آنتی اکسیدان می توان از 50 لیتر آب استفاده کرد.
سپس اتصالات از محلول خارج شده و با یک پارچه مرطوب پاک می شوند.
در مرحله بعد اتصالات را در محلولی از مخلوط پودر قلیایی و آب غوطه ور می کنند. در این محلول 1 کیلوگرم پودر را با 400 لیتر آب مخلوط کرده و فیتینگ را به مدت 5 دقیقه در این محلول گذاشته و سپس تمیز کرده و خارج کنید.
سپس ژل فسفات بلافاصله با استفاده از یک برس روی سطح میله ها اعمال می شود. بهتر است اجازه دهید این ژله به مدت 45 تا 60 دقیقه با سطح میلگرد واکنش نشان دهد و سپس آن را با آب بشویید یا از یک پارچه مرطوب استفاده کنید.
محلول ضد خوردگی با برس روی سطح آرمیچر اعمال می شود. محلول ضد خوردگی با سیمان پرتلند معمولی به میزان 500 سانتی متر مکعب در هر کیلوگرم مخلوط می شود تا دوغاب به دست آید. سپس این امولسیون با برس روی سطح آرمیچر اعمال می شود. تمام موارد فوق باید در یک روز انجام شود و میلگرد به مدت 12-24 ساعت خشک شود.
در نهایت در مرحله نهایی از درزگیر استفاده می شود. برای جلوگیری از خوردگی، یک درزگیر روی سطح آرمیچر اعمال می شود. این پوشش به مدت 4 ساعت پس از خشک شدن تکرار می شود.
6- پوشش همجوشی اپوکسی روی آرماتورهای فولادی
فرآیند پوشش اپوکسی کامپوزیت در پوشش مجدد طبق استاندارد IS: 13620 و فرآیند صنعتی در کارخانه ها انجام می شود. در صورت استفاده از پوشش اپوکسی، اطلاعات بیشتر در IS: 13620 باید در نظر گرفته شود. به طور کلی، فرآیند اعمال پوشش همجوشی اپوکسی در مقاوم سازی شامل مراحل زیر است:
سطح میلگرد فولادی را با مواد ساینده مانند سندبلاست تمیز کنید تا سطحی صاف و براق به دست آید. سطح میلگرد باید روشن، صاف، عاری از زنگ زدگی و مواد خارجی باشد. زیرا زنگ زدگی فرآیند چسبندگی پوشش را دشوار می کند.
پوشش مورد نظر باید در اسرع وقت روی سطح تمیز شده اعمال شود. زیرا حداکثر مدت زمان تمیز کردن قبل از شروع کار و اعمال پوشش هشت ساعت است.
این پوشش ها باید به عنوان یک پودر سخت رسانای الکتریکی که با استفاده از تفنگ پاشش الکترواستاتیک بر روی میلگرد فولادی پاشیده می شود، اعمال شود.
پودر را می توان به صورت گرم یا سرد استفاده کرد و ضخامت آن 0.1-33 میلی متر است.
میله تقویت کننده باید تحت عملیات حرارتی مشخص شده توسط سازنده قرار گیرد. همچنین میلگرد و دمای محیط باید کنترل شود تا از هر گونه شکستگی یا سایر عیوب جلوگیری شود.
پس از خشک شدن، عرشه میلگرد باید بازرسی شود و عاری از سوراخ، سوراخ، کثیفی، ترک و آسیب باشد.
مزایا و معایب میلگرد با پوشش اپوکسی
مزایا و معایب مواد پوشش اپوکسی
مهمترین ویژگی اتصالات با روکش اپوکسی خاصیت دی الکتریک و عایق بودن آنهاست. بنابراین یون کلرید نمی تواند از آن عبور کند و باعث خوردگی آرمیچر شود. همچنین این پوشش چسبندگی بالایی دارد و روی قسمت های آسیب دیده یراق آلات جدا نمی شود. از دیگر مزایای این نوع فیکسچر می توان به موارد زیر اشاره کرد:
انعطاف پذیری و انعطاف پذیری بالا در عملکرد ابزار
تمیز کردن سطح میلگرد ضروری نیست
معایب عمده میلگرد اپوکسی عبارتند از:
گران
اجرای کامل و بدون نقص روی میلگرد ضروری است
اگر پوشش آسیب دیده باشد و سوراخ هایی در آن ایجاد شود، اگر آرماتور صیقلی و ناهموار نباشد.
امکان آسیب دیدگی پوشش هنگام جابجایی میلگرد در کارخانه در طول حمل و نقل یا در حین تقویت
امکان آسیب به بتن مسلح در حین تراکم بتن
7- پشت نقاشی
یکی دیگر از روش های جلوگیری از خوردگی برد، به ویژه برای حفاظت از تاسیسات دریایی، رنگ آمیزی میلگرد است. استفاده از پوشش رنگ برای جلوگیری از خوردگی یکی از مقرون به صرفه ترین روش های جلوگیری از خوردگی است. پوشش رنگی به عنوان یک مانع برای جلوگیری از انتقال بار الکتروشیمیایی از محلول خورنده به فلز پایه عمل می کند.
استفاده از رنگ آمیزی جدا از صرفه اقتصادی، موثرترین و راحت ترین روش (از نظر دسترسی و تعمیر آسان) بوده و از سایر روش های نگهداری اهمیت بیشتری دارد. اعمال رنگ به صورت آستر و رویه، تا حدودی از تماس فلزات با محیط می کاهد و به نوبه خود از خوردگی میلگرد جلوگیری می کند. از بهترین رنگ های موجود می توان به رنگ های الکترواستاتیک و پوشش های فسفاته و کروماتی اشاره کرد.
8- میلگرد گالوانیزه
یکی از راه های تقویت آرماتور و جلوگیری از خوردگی آن، گالوانیزه کردن یا روکش کردن آرماتور است. این کار برای اتصالات با استفاده از تکنیک های گالوانیزه (الکترو گالوانیزه، گالوانیزه گرم، پوشش مکانیکی، پاشش روی و رنگ آمیزی رسی روی) اعمال می شود. با تشکیل یک پوشش گالوانیزه بر روی آرماتور، مقاومت آن در برابر خوردگی و اکسیداسیون به میزان قابل توجهی افزایش می یابد. کیفیت و ترکیب پوشش روی به طور مستقیم بر دوام و قابلیت اطمینان آن تأثیر می گذارد. همچنین این اتصالات در هنگام حمل و نقل دارای مشکلات کمی هستند. زیرا این پوشش از سطح فیکسچر محافظت می کند.
علاوه بر این، تحقیقات نشان می دهد که هنگام مواجهه با حمله کلرید، میلگرد گالوانیزه دومین گزینه مناسب پس از استفاده از میلگرد با روکش اپوکسی است.
نوک فیبر رزوه ای
در صورت استفاده از ترکیب قلع و میلگرد معمولی، خطر از بین رفتن پوشش تزئینی وجود دارد.
با توجه به قیمت بالای کابینت چوبی، در صورتی که مجبور به استفاده از میله های معمولی و موج دار هستید، باید بین این دو نوع میله، جداسازی کامل الکتریکی صورت گیرد.
استفاده از حفاظت الکتروشیمیایی (حفاظت کاتدی) در کنار سلاح های گالوانیزه با خطر بالایی همراه بوده و ممکن است خوردگی شدیدی رخ دهد.
9- اتصالات زنگ نزنند
برخی از آلیاژهای فولادی مانند فولاد ضد زنگ به دلیل استفاده از ترکیبات شیمیایی هستند که حاوی مقادیر زیادی کروم و نیکل هستند.