انجماد فلزات و آلیاژها
انجماد یک مرحله مهم در تشکیل فلزات و آلیاژها است، زیرا ریزساختار و خواص مواد حاصل را تعیین می کند. این فرآیند شامل تبدیل یک فلز مایع یا مذاب به حالت جامد از طریق خنک کردن یا وسایل دیگر است. انجماد می تواند به روش های مختلفی از جمله ریخته گری، جوشکاری و رسوب گذاری صورت گیرد. در این مقاله، ما در مورد انجماد فلزات و آلیاژها، اهمیت آن و عوامل موثر بر فرآیند بحث خواهیم کرد.
اولاً، انجماد فلزات و آلیاژها ضروری است زیرا خواص محصول نهایی را بسیار تحت تأثیر قرار میدهد. سرعت سرد شدن، جهت سرد شدن و دما همگی بر ریزساختار، اندازه دانه و ترکیب فاز ماده جامد شده تأثیر میگذارند. این عوامل می توانند تاثیر قابل توجهی بر خواص مکانیکی، الکتریکی و حرارتی فلز یا آلیاژ داشته باشند. بنابراین، کنترل فرآیند انجماد در دستیابی به خواص مطلوب برای یک کاربرد خاص بسیار مهم است.
ثانیاً انجماد فلزات و آلیاژها تحت تأثیر عوامل متعددی است. این عوامل عبارتند از سرعت سرد شدن، ترکیب آلیاژ، هسته و رشد کریستال ها و وجود ناخالصی ها. سرعت سرد شدن بسیار مهم است زیرا بر سرعت تشکیل کریستال ها نظارت می کند که اندازه دانه و جهت گیری را تعیین می کند. ترکیب آلیاژ بر دامنه انجماد، تعداد فازها و مورفولوژی آن ها تأثیر می گذارد. هسته زایی و رشد به طور همزمان در طول فرآیند انجماد اتفاق می افتد و اندازه، شکل و توزیع ذرات جامد را کنترل می کند. در نهایت، وجود ناخالصیها میتواند با ترویج هستهزایی، تغییر سرعت رشد و تغییر انواع فازهای تشکیلشده، بر انجماد تأثیر بگذارد.
ثالثاً، انجماد می تواند از طریق روش های مختلفی مانند ریخته گری، جوشکاری و رسوب گذاری صورت گیرد. ریخته گری پرکاربردترین روش است و شامل ریختن فلز مایع در قالب و اجازه دادن به خنک شدن و جامد شدن آن است. جوشکاری شامل ذوب فلز و انجماد مجدد آن برای اتصال دو قطعه ماده است. رسوب دهی فرآیندی است که شامل رشد کنترل شده یک لایه نازک فلز از طریق تکنیک های رسوب در فاز بخار است. هر یک از این روش ها مزایا و معایب متفاوتی دارند و می توان آن ها را برای دستیابی به خواص مطلوب مواد بهینه کرد.
در نتیجه، انجماد فلزات و آلیاژها فرآیندی حیاتی است که بر ریزساختار و خواص مواد حاصل تأثیر می گذارد. سرعت سرد شدن، جهت سرد شدن و دما از جمله عواملی هستند که بر انجماد تأثیر میگذارند که میتواند از طریق تکنیکهای مختلفی مانند ریختهگری، جوشکاری و رسوبگذاری انجام شود. کنترل فرآیند انجماد در دستیابی به خواص مطلوب ماده برای یک کاربرد خاص بسیار مهم است. بنابراین شناخت اصول انجماد و عوامل موثر بر آن در تولید و بهینه سازی خواص فلزات و آلیاژها ضروری است.
معرفی:
انجماد فلزات و آلیاژها فرآیند مهمی در ساخت محصولات مختلف است. به انتقال یک ماده از حالت مایع به حالت جامد اشاره دارد. این فرآیند در کاربردهای مختلفی مانند ریختهگری، جوشکاری و ساخت مواد افزودنی استفاده میشود. فرآیند انجماد می تواند بر خواص مواد مانند استحکام، شکل پذیری و چقرمگی تأثیر بگذارد. در این مقاله به انجماد فلزات و آلیاژها و اهمیت آن در فرآیند ساخت می پردازیم.
فرآیند انجماد:
فرآیند انجماد فلزات و آلیاژها در چند مرحله انجام می شود. ابتدا فلز مذاب شروع به سرد شدن کرده و هسته های جامد تشکیل می دهد. در مرحله بعد، این هسته های جامد رشد کرده و با یکدیگر ترکیب می شوند تا زمانی که یک ساختار جامد را تشکیل دهند. مرحله آخر سرد شدن فلز تا دمای نهایی آن است. بسته به سرعت سرد شدن و سایر عوامل، ساختار نهایی فلز می تواند کریستالی یا بی شکل باشد.
اهمیت انجماد:
فرآیند انجماد یک مرحله اساسی در تولید است. معمولاً در ریختهگری اشکال پیچیده مانند پرههای توربین، بلوکهای موتور و سایر قطعات استفاده میشود. همچنین در تولید پودرهای فلزی مورد استفاده در تولید مواد افزودنی حیاتی است. فرآیند انجماد ریزساختار ماده را تعیین می کند که بر خواص مکانیکی و فیزیکی آن تأثیر می گذارد. به عنوان مثال، سرعت سرد شدن آهسته میتواند منجر به دانههای بزرگتر، افزایش شکلپذیری و کاهش استحکام شود، در حالی که سرعت خنکسازی سریع میتواند دانههای کوچکتر، استحکام بیشتر و کاهش شکلپذیری ایجاد کند.
انجماد آلیاژی:
آلیاژها به مخلوط دو یا چند فلز یا یک فلز و یک نافلز اطلاق می شود. انجماد یک آلیاژ فرآیندی پیچیده تر از انجماد فلزات خالص است. ساختار یک آلیاژ با ترکیب و سرعت خنک شدن آن تعیین می شود. انجماد یک آلیاژ می تواند منجر به طیفی از ریزساختارها شود که بر خواص مکانیکی مواد تأثیر می گذارد. در برخی موارد، آلیاژسازی ممکن است خواص مواد مانند استحکام، چقرمگی و شکل پذیری را افزایش دهد.
نتیجه:
در نتیجه، انجماد فلزات و آلیاژها نقش مهمی در فرآیند تولید دارد. این ریزساختار یک ماده را تعیین می کند که می تواند بر استحکام، شکل پذیری و چقرمگی آن تأثیر بگذارد. فرآیندهای مختلف ریختهگری، تکنیکهای تولید افزودنی و روشهای جوشکاری از فرآیند انجماد استفاده میکنند. درک صحیح از انجماد فلزات و آلیاژها برای طراحی مواد با خواص خاص بسیار مهم است و در نتیجه آن ها را در کاربردهای مختلف مفید میسازد.
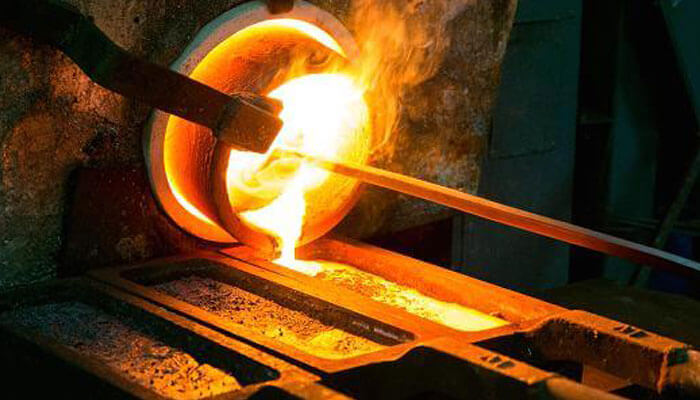
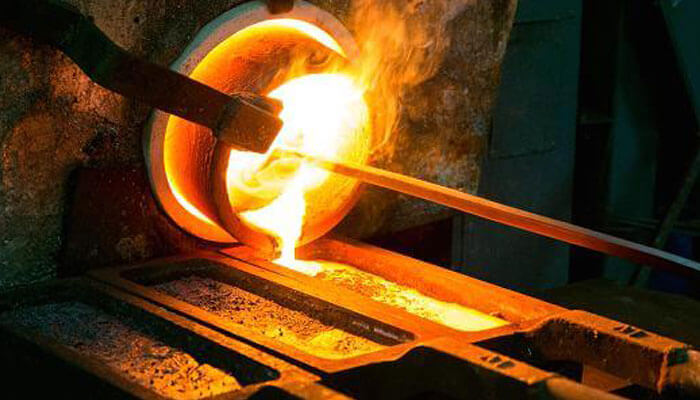
انجماد فلزات و آلیاژها
نکات مهم انجماد فلزات و آلیاژها
انجماد یک فرآیند حیاتی برای فلزات و آلیاژها است که به دستیابی به خواص مطلوب مانند استحکام، چقرمگی و شکل پذیری کمک می کند. این فرآیند شامل تبدیل فلز مذاب یا آلیاژ به حالت جامد است. با این حال، انجماد می تواند به دلیل عوامل متعددی مانند ترکیب آلیاژ و سرعت خنک شدن پیچیده باشد. هدف این مقاله بررسی نکات مهم انجماد فلزات و آلیاژها است.
اولین نکته مهم انجماد، فرآیند هستهزایی است. هسته سازی به تشکیل کریستال ها در طول فرآیند خنک سازی اشاره دارد. این شامل تجمع اتم ها یا مولکول ها برای تشکیل یک ساختار بلوری پایدار است. بسته به دما و سرعت سرد شدن، هسته زایی می تواند به صورت همگن یا ناهمگن رخ دهد. هستهزایی همگن زمانی اتفاق میافتد که دما زیر نقطه ذوب باشد و سرعت هستهزایی کندتر باشد. از سوی دیگر، هستهزایی ناهمگن زمانی اتفاق میافتد که مواد خارجی بهعنوان مکآن های هستهزایی عمل کرده و فرآیند انجماد را تسریع میکنند.
دومین نکته مهم انجماد اندازه و شکل دانه ها است. اندازه و شکل دانه ها به طور قابل توجهی بر خواص فلزات و آلیاژها تأثیر می گذارد. دانه های بزرگتر استحکام کمتری را نشان می دهند، در حالی که دانه های کوچکتر استحکام، چقرمگی و شکل پذیری بالاتری دارند. شایان ذکر است که اندازه و شکل دانه ها با سرعت سرد شدن، ترکیب آلیاژ و شرایط انجماد تعیین می شود.
سومین نقطه مهم انجماد، جداسازی عناصر است. در طول انجماد، یک گرادیان غلظت می تواند در آلیاژ ایجاد شود که باعث تغییر در ترکیب آلیاژ می شود. این جداسازی می تواند منجر به خواص نامطلوب مانند خوردگی یا شکنندگی شود. بنابراین کنترل سرعت سرمایش و حفظ توزیع همگن عناصر بسیار مهم است.
چهارمین نکته ضروری انجماد، ایجاد عیوب مانند ترک، حفره و آخال است. این عیوب می توانند بر خواص مکانیکی آلیاژ تأثیر بگذارند و استحکام، چقرمگی و شکل پذیری را کاهش دهند. وجود عیوب معمولاً به دلیل شرایط انجماد نامناسب از جمله دما، سرعت سرد شدن یا ناخالصی ها است. بنابراین، اجتناب از این شرایط برای دستیابی به خواص مطلوب بسیار مهم است.
پنجمین و آخرین نکته ضروری انجماد، پس پردازش است. پس پردازش بخش مهمی از انجماد است که شامل پردازش فلز یا آلیاژ برای دستیابی به خواص مکانیکی، فیزیکی و شیمیایی مورد نظر است. پس پردازش می تواند شامل عملیات حرارتی یا کار مکانیکی مانند نورد سرد یا آهنگری برای بهبود خواص مکانیکی آلیاژ باشد.
در نتیجه، انجماد نقش حیاتی در دستیابی به خواص مطلوب برای فلزات و آلیاژها دارد. نکات مهم انجماد مورد بحث در این مقاله شامل هستهزایی، اندازه و شکل دانهها، جداسازی عناصر، تشکیل عیوب و پسفرآوری است. با درک این نکات ضروری، مهندسان می توانند آلیاژهایی را با خواص بهینه طراحی و تولید کنند که برای کاربردهای مختلف ضروری است.
انجماد یک فرآیند ضروری در تولید فلزات و آلیاژها است. این فرآیند شامل انتقال حالت مذاب به حالت جامد است. انجماد فلزات و آلیاژها به دلیل سرد شدن مواد رخ می دهد که منجر به تشکیل آرایش منظم اتم ها می شود. درک فرآیند انجماد فلزات و آلیاژها بسیار مهم است زیرا بر خواص فیزیکی آن ها مانند استحکام، سختی و شکل پذیری تأثیر می گذارد. این مقاله به نکات مهم مربوط به انجماد فلزات و آلیاژها می پردازد.
یکی از مفاهیم کلیدی در انجماد فلزات و آلیاژها، هسته زایی است. هسته سازی به تشکیل یک کریستال جدید در یک ماده اشاره دارد. هنگامی که یک فلز یا آلیاژ مذاب در زیر نقطه ذوب سرد می شود، اتم ها حرکت تصادفی خود را متوقف می کنند و شروع به تشکیل آرایش های مرتب می کنند. فرآیند انجماد با تشکیل ساختارها یا هسته های کریستالی ریز آغاز می شود. این هستهها با اضافه شدن اتمهای بیشتر و بیشتر برای تشکیل ساختار شبکه جامد رشد میکنند. هسته زایی یک فرآیند حیاتی است زیرا اندازه و شکل دانه را تعیین می کند که به نوبه خود بر خواص مکانیکی و فیزیکی مواد تأثیر می گذارد.
یکی دیگر از مفاهیم حیاتی در فرآیند انجماد، سردسازی کم است. سرد شدن کم زمانی اتفاق می افتد که یک ماده در زیر نقطه ذوب خود بدون انجماد به خنک شدن ادامه دهد. سیستم سرد نشده حالت مایع خود را حفظ می کند زیرا تشکیل هسته ها به اندازه بحرانی انرژی آزاد نیاز دارد. انرژی مورد نیاز برای تشکیل هسته با کاهش دما افزایش می یابد و در برخی مواقع، سیستم نمی تواند انرژی کافی برای تشکیل کریستال جدید را تامین کند. با این حال، سرد شدن کم منجر به هستهزایی سریع و تشکیل مواد ریزدانه میشود که دارای استحکام بالاتر و خواص مکانیکی بهبود یافتهاند.
نرخ سرد شدن عامل مهم دیگری است که بر فرآیند انجماد تأثیر می گذارد. سرعت سرد شدن سریع منجر به تشکیل دانه های ریز می شود، در حالی که سرعت سرد شدن آهسته منجر به تشکیل دانه های درشت می شود. سرعت سرد شدن بر انتشار اتم ها و رشد هسته ها تأثیر می گذارد. انتشار اتم ها در دماهای بالا سریعتر است، در حالی که سرعت سرد شدن آهسته منجر به نرخ انتشار کمتر می شود. سرعت سرد شدن نیز بر تشکیل عیوب کریستالی مانند جاهای خالی و دررفتگی تأثیر می گذارد که می تواند بر خواص مکانیکی مواد تأثیر بگذارد. سرعت سرد شدن سریع می تواند یک ماده را خاموش کند، خواص آن را تغییر دهد و منجر به تشکیل جامدات آمورف شود.
در نهایت، عناصر آلیاژی بر فرآیند انجماد فلزات و آلیاژها تأثیر میگذارند. عناصر آلیاژی رفتار ذوب و انجماد فلز را تغییر می دهند و موادی با خواص بهبود یافته تولید می کنند. افزودن عناصر آلیاژی به یک ماده می تواند منجر به تشکیل ساختارهای یوتکتیک شود که می تواند برای خواص مواد مفید یا مضر باشد. ساختار یوتکتیک از واکنش بین فاز مایع و جامد در نقطه یوتکتیک به وجود می آید. ساختارهای یوتکتیک می توانند خواص مکانیکی مواد مانند چقرمگی و مقاومت در برابر سایش را بهبود بخشند.
در نتیجه، درک فرآیند انجماد فلزات و آلیاژها در تولید مواد با خواص بهبود یافته ضروری است. هسته زایی، سرد شدن کم، سرعت خنک سازی و
تأثیر انجماد فلزات و آلیاژها بر کیفیت آن ها
فلزات و آلیاژها به دلیل ویژگی ها و ویژگی های منحصر به فرد خود معمولاً در صنایع مختلف مورد استفاده قرار می گیرند. این مواد تحت تکنیک های مختلف پردازش از جمله انجماد قرار می گیرند. انجماد یک تکنیک حیاتی است که برای تثبیت فلزات و آلیاژها و بهبود کیفیت آن ها استفاده می شود. انجماد می تواند بر کیفیت فلز و آلیاژ به طرق مختلف بسته به کاربرد خاص تأثیر بگذارد.
اولین اثر انجماد فلز و آلیاژها، تشکیل ریزساختار است. در طی فرآیند انجماد، مواد جامد میشوند و حرکت اتمی را مهار میکنند و در نتیجه ساختار بلوری را حفظ میکنند. در نتیجه، ماده دچار تغییرات پیوند اتمی می شود که اغلب منجر به تشکیل کریستال های منحصر به فرد می شود. ساختار کریستالی تازه تشکیل شده منجر به تغییراتی در خواص مکانیکی مواد مانند استحکام کششی و سختی می شود. بنابراین، انجماد به متالورژیستها اجازه میدهد تا ویژگیهای مواد مانند اندازه دانه را از طریق هستهزایی مورفولوژیهای مختلف کریستال تغییر دهند، که سپس بر خواص ساختار و در نتیجه بر کیفیت فلز یا آلیاژ تأثیر میگذارد.
دومین اثر قابل توجه انجماد فلزات و آلیاژها بر مقاومت آن ها در برابر خوردگی است. فلزاتی که تحت فرآیند انجماد قرار می گیرند اغلب مقاومت در برابر خوردگی بهبود یافته ای را نشان می دهند. مقاومت در برابر خوردگی از آنجایی رخ می دهد که فرآیند انجماد می تواند به حداقل رساندن جداسازی عناصر در طول تشکیل رشد دندریتی کمک کند. اگر فلزی در معرض سرد شدن یا خاموش شدن سریع قرار گیرد، میتواند شکاف ایجاد کند یا باعث جدا شدن عناصر شود و بر کیفیت آن تأثیر بگذارد. با این حال، خنک شدن آهسته به طور قابل توجهی این اثر منفی را با اجازه دادن به برخی از عناصر برای انتشار در مناطق دیگر به حداقل می رساند و در نتیجه جداسازی عناصر را کاهش می دهد.
یکی دیگر از نتایج کلیدی انجماد فلزات و آلیاژها بهبود خواص مکانیکی است. انجماد معمولا برای بهبود خواص مکانیکی خاص مانند شکل پذیری و استحکام فلزات و آلیاژها استفاده می شود. بسته به کاربرد خاص، مواد می توانند تحت فرآیندهای بازپخت و کوئنچ قرار گیرند تا خواص مکانیکی خاص را افزایش دهند. به عنوان مثال، فلزاتی مانند فولاد که در معرض خاموش شدن سریع قرار می گیرند منجر به تشکیل مارتنزیت می شوند. این دگرگونی منجر به افزایش سختی قطعات خودرو و نیروگاه و در نتیجه بهبود کیفیت می شود.
علاوه بر این، انجماد می تواند به طور قابل توجهی ماشین کاری و کارایی فلزات و آلیاژها را بهبود بخشد. با قرار دادن فلزات در معرض انجماد سریع، آن ها دستخوش تغییرات فاز پیچیده ای می شوند که می تواند بر ماشین کاری و کارایی آن ها تأثیر بگذارد. انجماد اغلب با جلوگیری از تغییر شکل در طی فرآیند ماشینکاری، شکل پذیری فلز را بهبود می بخشد. فلزات سرد کار معمولاً دارای استحکام و سختی بالایی هستند. با این حال، این ویژگی ها اغلب به قیمت ماشین کاری ضعیف انجام می شود. بنابراین، انجماد می تواند به از بین بردن این موضوع کمک کند و منجر به بهبود کارایی شود.
در نتیجه، تأثیر انجماد فلزات و آلیاژها بر کیفیت آن ها تأثیر بسزایی در کاربردهای صنعتی متعدد دارد. کیفیت فلز و آلیاژ را می توان از طریق تشکیل ریزساختار، افزایش مقاومت در برابر خوردگی، بهبود خواص مکانیکی و افزایش قابلیت ماشینکاری و کارایی بهبود بخشید. بنابراین، تولیدکنندگان آلیاژها و فلزات برای افزایش کیفیت و پایداری محصولات خود باید درک جامعی از اثرات تکنیک های انجماد داشته باشند. علاوه بر این، تحقیقات بیشتری باید انجام شود تا چگونگی واکنش آلیاژها و فلزات مختلف به تکنیکهای مختلف انجماد برای به حداکثر رساندن فواید انجام شود.
انجماد فلزات و آلیاژها در صنایع مختلف برای بهبود کیفیت آن ها استفاده شده است. فرآیند انجماد شامل سرد کردن فلز یا آلیاژ تا دمایی کمتر از نقطه انجماد آن است که باعث میشود اتمها خود را در یک الگوی منظمتر مرتب کنند. این فرآیند می تواند به طور قابل توجهی بر کیفیت فلز یا آلیاژ تأثیر بگذارد.
اولین اثر انجماد فلزات و آلیاژها بهبود استحکام و دوام آن هاست. بازآرایی اتم ها در فلز یا آلیاژ در طول فرآیند انجماد ساختار منظم تری ایجاد می کند. ساختار سفارش داده شده استحکام مواد را بهبود می بخشد و آن را بادوام تر می کند و قادر به تحمل شرایط شدید است. این بهبود در استحکام و دوام به ویژه برای فلزات و آلیاژهای مورد استفاده در صنایعی مانند ساخت و ساز، هوانوردی و حمل و نقل، که در آن مواد باید در برابر تنش ها و دماهای شدید مقاومت کنند، قابل توجه است.
ثانیا، انجماد فلزات و آلیاژها می تواند مقاومت آن ها را در برابر خوردگی بهبود بخشد. خوردگی مشکل عمده ای است که فلزات و آلیاژها، به ویژه آن هایی که در محیط های سخت استفاده می شوند، با آن مواجه هستند. انجماد فلزات و آلیاژها با کاهش تحرک اتم های فلز، سرعت خوردگی را کاهش می دهد و واکنش آن ها را با محیط سخت تر می کند. این امر مقاومت در برابر خوردگی فلز را بهبود می بخشد و آن را برای صنایعی که به موادی با مقاومت در برابر خوردگی بالا نیاز دارند، مانند صنایع دریایی و نفت و گاز، انتخابی ارجح تبدیل می کند.
ثالثاً، انجماد فلزات و آلیاژها می تواند ثبات ابعادی آن ها را بهبود بخشد. پایداری ابعادی به توانایی فلز یا آلیاژ برای حفظ شکل و اندازه خود در شرایط دمایی مختلف اشاره دارد. فرآیند انجماد به تثبیت اتمهای فلز یا آلیاژ کمک میکند و کمتر مستعد انبساط، انقباض یا تاب برداشتن میشود که میتواند به دلیل تغییرات دما رخ دهد. این امر آن را برای صنایعی که به موادی با ثبات ابعادی بالا نیاز دارند، مانند صنایع الکترونیک و هوافضا، انتخابی ارجح تبدیل می کند.
با این حال، فرآیند انجماد فلزات و آلیاژها نیز دارای معایبی است. یکی از نکات منفی قابل توجه احتمال شکنندگی است. بازآرایی اتم ها در طول فرآیند انجماد می تواند شکاف ها یا حفره های کوچکی ایجاد کند که می تواند فلز یا آلیاژ را شکننده کند و خواص مکانیکی کلی آن را کاهش دهد. این یک نگرانی عمده است، به ویژه برای موادی که به چقرمگی بالا نیاز دارند، مانند مواردی که در صنایع خودروسازی و هوافضا استفاده می شود.
در نتیجه، انجماد فلزات و آلیاژها می تواند به طور قابل توجهی کیفیت آن ها از جمله استحکام، دوام، مقاومت در برابر خوردگی و پایداری ابعادی آن ها را بهبود بخشد. با این حال، فرآیند انجماد نیز دارای معایبی است، از جمله احتمال شکنندگی. در نهایت، تصمیم به انجماد فلز یا آلیاژ باید پس از بررسی کامل کاربرد مورد نظر و عواقب احتمالی آن اتخاذ شود. اهمیت وزن کردن مزایا و معایب این فرآیند را نمی توان نادیده گرفت زیرا می تواند تأثیرات قابل توجهی بر کیفیت نهایی و خواص مواد داشته باشد.